Table of Contents
![]() Original Clarkson Feeder |
![]() Clarkson Feeders |
![]() |
The Clarkson Company had once designed a combination drum and scoop type liquid reagent feeder, the largest size of which has a capacity rating of 2000 tons of dry ore per 24 hr. This will enable the feeder to take a large tonnage of initial feed and several hundred per cent, circulating load as well. The drum of the large feeder is 48 in. in diameter and allowance is provided for a scoop with a radius of 48 or 54 in., as may be required by the customer. All parts are reversible, which means that the purchaser no longer has to specify which way his mill is rotating when buying a feeder.
It also enables him to reduce his stock when he has mills rotating in the opposite direction, as, by merely changing the parts, the same feeder can be used on a mill rotating in clockwise or counter-clockwise direction. Parts are made replaceable to take care of ordinary wear and the cost of renewing parts is therefore very small. The advantages of a combination of drum and scoop type feeder are well known. Such feeders as this have been used for a number of years on the larger mills handling in excess of 500 tons per 24 hr. and have proved practical, as the wear is light and they cause no mechanical trouble.
These machines have because rare and expensive, costing you (new) from $3500 to $4500 depending who you deal with.
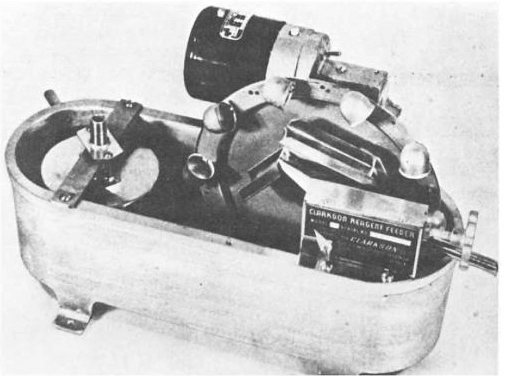
The Clarkson bucket feeder.This has small buckets mounted on a vertical rotating disc, which dip into the liquid in the tank and spill out their contents on to a tipping plate on each revolution. The feed rate can be varied by adjusting the speed, the size of buckets, or more commonly, in operation, the angle of tilt of the plate, which governs the amount of liquid returned to the tank. A number of discs can be driven from one shaft, each dispensing a different reagent from a separate compartment in the tank.
Insoluble liquids such as pine oil are often fed at full strength, whereas water soluble reagents are made up to fixed solution strengths, normally about 10%, before addition. Reagent mixing is performed on day shift in most mills, under close supervision, to produce a 24-h supply. The aqueous reagents are usually pumped through ring-mains, from where they are drawn off to feeders as required.
Liquid Reagent Distribution System
The addition of solid reagents to the circuit is effected by a miniature belt feeder controlled by a variable speed device.
Lime is sometimes added to the circuit as a solid, but the more satisfactory and usual method is to grind it with a definite proportion of water in a small ball mill, and, after removing any solid particles, to feed the milk of lime through a valve nearly full open and therefore unlikely to choke.
A mechanical cup feeder, as illustrated in Fig. 30, is the commonest type used for liquid reagents and solutions ; the covered apparatus designed to handle aerofloat is made of non-corrosive material. It consists of a tank on which is mounted a metal disc driven at ½ to 4 r.p.m. by a small motor fitted with some device for varying the speed. Small cups are suspended from bolts round the periphery of the disc in such a way that they swing freely without being able to move laterally on the bolts. At the lowest point of their travel the cups are submerged in the reagent contained in the tank ; they are carried up as the disc revolves until they reach a tripper arm which can be adjusted to tip out any required quantity of liquid. The bolts which hold the cups are of different lengths, and the sliding discharge trough can be shifted in or out to take the contents of any number of cups from one upwards These adjustments give the feeder a very wide range.
For plant work several feeders are usually connected to one motor and placed in some central spot well above the points where the reagents are required to enter the circuit.
Reagent Distributor (Lewers Type)
The Reagent Distributor is an accessory machine to the Wet Reagent Feeder. It accurately distributes the reagents from the feeder to every cell in the flotation circuit in precisely the proper quantities to give the highest efficiency possible.
The value of “step oiling” has long been realized by millmen, but operating difficulties have discouraged the practice. The reagent distributor fills this requirement and is simple to control. The reagent from the reagent feeder (plus enough water to make a steady stream) passes to the revolving head of the distributor where the reagent and water are mixed and pass under a baffle to the discharge pipe in the center.
From this pipe the liquid flows to the discharge spout which is revolving with the head. The trough which receives this liquid is circular and can be divided easily into a number of different sized compartments by removable and adjustable partitions. From the bottom of each compartment a pipe leads to the desired flotation cell, as many as twenty-six of which can be fed from this central distributor, which requires practically no power. A small inexpensive distributor is also available where only a few distributing branches are desired. These units can be furnished either belt or motor driven.
Reagent Distributor Capacity