Table of Contents
Large scale mining and processing of phosphate is essential for operating at a profit. In the Florida area, Phosphate Beneficiation by flotation unlocked the door to vast tonnages of ore which in the past could not be recovered by conventional washing methods which saved only the coarser pebble phosphate. Many of the areas now being mined contain very little or no pebble phosphate, so the main recovery is from the fine sands.
In the treatment of phosphatic shales for recovery of phosphate, a simple low cost flexible flowsheet is highly desirable. Since all grades of ore from low to high P2O5 content may occur in a deposit it is important to consider the possibility of either mixing the ores or to segregate them into grades for separate treatment. Laboratory and pilot plant work is very valuable in establishing the final treatment which will give the maximum net economic return.

The Phosphate Beneficiation Flowsheet
Phosphate Ore Mining
Electrically operated drag lines strip off the overburden from the mining area and deposit the phosphate matrix around a pump pit. Here it is sluiced with streams of high pressure water to the suction of a large centrifugal pump which transports the matrix slurry to the washing plant which may be a mile or two away.
Washing and Screening Phosphate Rock
At the washer the water-matrix slurry discharges into a surge receiving bin or tub and is screened for removal of clay, sand and fine phosphate from the mud balls. The screen oversize passes through a hammer mill to break down the mud balls and occasional large pebbles. The screen undersize and disintegrated mud balls pass to a pebble washing and screening section consisting of a trommel screen and log washer. Here, clean washed pebble phosphate—usually —½” plus 14 mesh, depending upon the character of matrix being mined—is removed. Tramp oversize is recycled to the hammer mill for further disintegration, and —14 mesh matrix slurry passes to the fine recovery section.
“Sub-A” Flotation Machine (Phosphate Type). Please note free-flow of pulp for fast-floating ore and high tonnage
operation. Shaft assembly is removable as one unit. Repeated pulp circulation (as indicated) assures proper agitation and
aeration. Supercharged air can be added down standpipe or down hollow shaft, or both, as conditions require.
Classification and Desliming Phosphate
Following removal of the pebble, the balance of the ore or matrix flows by gravity to a large hydroclassifier for separation of the sands from the slimes at 150 mesh. The —150 mesh slimes containing the colloidal clay, very fine silica and phosphate are discarded.
Fines are removed from the storage bins by a centrifugal pump, fed through pinch valves and regulated by high pressure water jets. The pump discharges into a spiral or rake classifier, the overflow going to a secondary hydroclassifier, and the sands to a hydraulic classifier. This classification system splits out a +20 mesh pebble phosphate, a —20 +35 mesh fraction for agglomerate separation, and —35 mesh which is the feed to flotation. All classifier overflow and excess water accumulated in the washing steps are diverted back to the large primary hydroclassifier for retreatment. Wet cyclones can be successfully applied in the classification systems to eliminate slime and excess water from the fines.
Agglomerate Separation of Phosphate
The —20 +35 mesh phosphate-sand mixture is further deslimed and conditioned with reagents at high density, 70-75% solids in a rotary drum type conditioner. The phosphate particles are filmed with the fuel oil, fatty acid, caustic mixture which renders them non- wettable. This coarse pulp then is subjected to tabling, spiraling, or belt agglomerate treatment which separates the phosphate from the silica particles. This usually produces a finished, high grade phosphate concentrate and a clean waste product. In some cases it may be necessary to clean the phosphate product by silica flotation, as indicated by the alternate flow lines.
Phosphate Conditioning and Fatty Acid Flotation
The —35 mesh matrix is fed from the fine recovery bins to a rake or spiral classifier for further desliming, and the sands at high density, 65 to 70% solids, are introduced in a Heavy Duty Open Type Duplex Phosphate Conditioner. Two or more conditioning tanks are generally used in series. Caustic soda, fuel oil, and tall oil are metered to the conditioner feed and agitated to thoroughly film all the phosphate particles.
The discharge from the conditioning circuit is diluted down to about 25% solids and fed directly to a “Sub-A” Flotation Machine. Since tonnages are high, usually in excess of 100 long tons per hour to each circuit, the No. 30 (56×56) “Sub-A” Flotation Machine—having 100 cubic ft. of volume per cell—is standard for the fatty acid flotation separation. Phosphate is removed in the froth product and the silica passes out the end of the machine to waste. Flotation is very rapid when the feed is properly conditioned and metered to the machine. Usually at least 4 cells are used in series for each circuit. In some cases, one stage of cleaning is necessary to produce an acceptable grade in the fatty acid flotation section. Grade is usually 68 to 72% BPL (Bone Phosphate of Lime).
Neoprene wearing parts are necessary to withstand the action of the fatty acid-fuel oil flotation reagents and large adjustable sand reliefs are standard in the Cells for phosphate flotation. Because of the high percentage of phosphate to be removed in the froth product, a double overflow machine with froth paddles is standard. Supercharging improves performance and reduces power requirements for flotation.
Silica Flotation
Usually, when it is necessary to produce concentrates having 72-78% BPL, the fatty acid flotation concentrate is subjected to reverse flotation in which the phosphate is depressed and the silica contaminant activated and floated in a separate circuit.
The fatty acid froth product, in this case, flows by gravity to another set of Heavy Duty Acid Proof Conditioners. These are neoprene lined. Sufficient concentrated sulphuric acid is added to the pulp to produce a low acid pH. This cuts and removes the fatty acid reagents from the phosphate particles. The reagent and acid water is removed by thorough washing and desliming. The classifier sand product containing the de-activated phosphate and silica impurity passes to a second “Sub-A” Flotation Circuit for removal of silica in a froth product. Cationic reagents, such as amine acetate, are used to activate and float the silica.
In some circuits, the phosphate concentrate from the coarse agglomerate separation section, if not high enough grade, is introduced into the silica flotation section along with the product from the fatty acid flotation section. This is done when a high purity product, usually 76-78% BPL, is required. The flotation circuits are set up for maximum flexibility to accommodate changes in tonnage and character of feed as well as requirements on the finished products.
Recovery of Phosphate
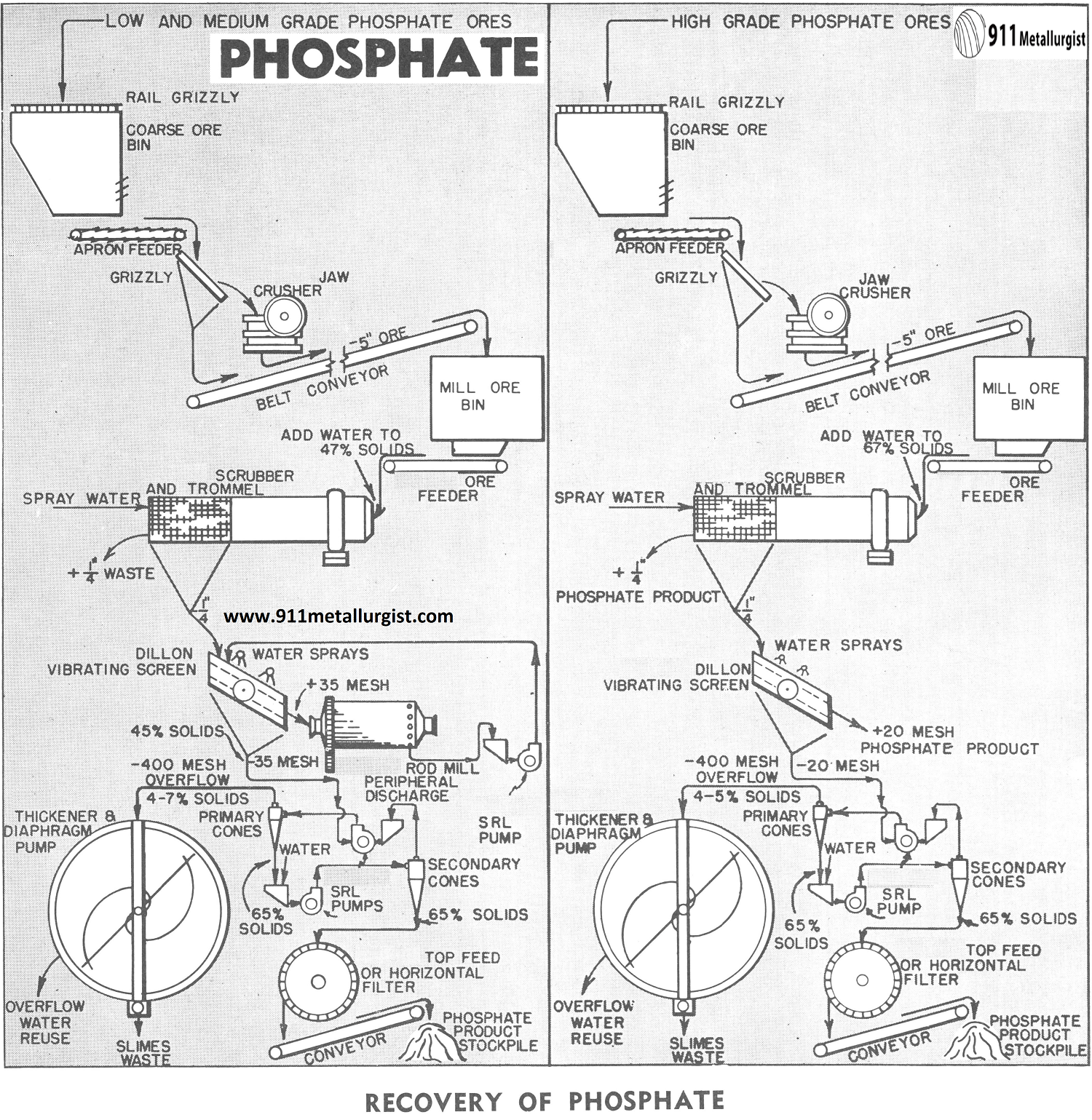
In the treatment of phosphatic shales for recovery of phosphate, a simple low cost flexible flowsheet is highly desirable. Since all grades of ore from low to high P2O5 content may occur in a deposit it is important to consider the possibility of either mixing the ores or to segregate them into grades for separate treatment. Laboratory and pilot plant work is very valuable in establishing the final treatment which will give the maximum net economic return.
Solution of the Phosphate Problem
Extensive tests have established that where mining can be controlled the ores should be selectively mined and treated as two distinct operations, namely: to produce ore with a low or medium phosphate content and an ore with high phosphate content. For the low grade and medium grade ores, containing 18 to 22% P2O5, generally a coarse waste product can be produced and rejected. Treatment of the high grade ores containing about 28% P2O5 will generally result in the production of a coarse phosphate product. This is in addition to production of granular fines as an acceptable phosphate and a slime waste product.
The Flowsheet for Phosphate Beneficiation
In the foregoing flowsheets, two parallel systems are shown for the treatment of both low and high grade ores separately.
CRUSHING AND STORAGE
In case only one crusher is used for both types of ore, the crushing period can be divided to accommodate the respective tonnages. Usually crushing is confined to one or two shifts per day, depending upon the size of the operation.
SCRUBBING AND SCREENING
Water is added to give a feed density of approximately 67% solids. Retention time in the scrubber is important to thoroughly break down and scour the slime from the ore. Retention time will vary from 5 to 30 minutes depending upon the grade and character of the ore. The scrubbed ore passes the trommel section of the scrubber where the +¼” oversize is removed. Sprays are applied to give a clean oversize product.
In the case of low and medium grade phosphatic shale ores the + ¼” fraction is low grade and is rejected as a waste product. This usually amounts to 9-10% of the feed tonnage. The high grade ores, on the other hand, when treated in this manner, give an oversize product +¼” sufficiently high in P2O5 content to be a finished product. About 8% of the weight represents this fraction of acceptable product +¼” size.
In the case of the low grade ores, the screening is done at 35 mesh. The screen oversize +35 mesh is usually not a finished product and therefore requires further grinding. High grade ores will generally produce an acceptable product at +20 mesh without further treatment.
ROD MILLING
Low grade -¼” to 35 mesh screened and washed oversize is reduced to minus 35 mesh in a pheripheral discharge Rod Mill which is in closed circuit with the vibrating screen. An elevator or SRL Pump can be used to transfer the mill discharge to the screen. The rod mill action polishes off the softer shale fraction from phosphate particles and keeps sliming of phosphate to a minimum. The feed to the rod mill will approximate 12% of the initial feed tonnage.
CLASSIFICATION
Extensive pilot plant tests have shown that wet cyclones provide a very efficient method for removal of slimes which are largely minus 400 mesh. The slimes, so produced, are low in P2O5 content and are discarded to waste. Two stages of cones are required and the underflow from the secondary stage constitute a final product ready for filtration.
In the case of low and medium grade ores, the — 35 mesh cone feed represents about 90% of the plant tonnage and will reject 35 to 36% as slimes to waste. The —20 mesh feed for high grade ores represents about 85% of the plant tonnage and the overflow to waste will be about 15 to 16%. Underflow from the primary cones constitutes feed to the secondary cones.
Secondary cones in the case of low and medium grade ores, receive 62% of the initial plant feed. The overflow is recycled back to the primary cone feed. The overflow fraction amounts to 6-7% of the original plant feed. The underflow, representing about 55% of the plant feed at 65% solids, is ready for filtration. In the case of high grade ores, the secondary cone feed is about 70% and the recycled overflow is about 4% The underflow product representing 65 to 66% at 65% solids is fed to the filter.
No water needs to be added to the primary cone pump sump. Water is necessary in the secondary cone feed pump and the resulting cone overflow then becomes dilution for the primary cone circuit. Primary cone overflow will vary between 4 and 8% depending upon the type of ore being treated.
Phosphate FILTRATION
The discharge from the secondary cones is a slime free granular product containing about 65% solids. This is ideal filter feed, but it is necessary to use a top feed or horizontal filter for efficient de-watering.
THICKENING Phosphate
The slime overflow from the primary cones at 4 to 8% solids is fed to a thickener for water reclamation. The slimes will settle to about 25% solids and are pumped from the underflow to tailing ponds. Special precautions should be taken when impounding this material due to the almost complete absence of sand. Several separate ponds may be necessary to store this waste.
WATER REQUIREMENTS
With reclamation of plant water from the slime tailing in a thickener, the amount of new water for low and medium grade ores will be about 300 gallons per ton of ore treated. High grade ores require about 150 gallons per ton. This is well within the range of average mill water requirements when reclamation is a part of the system.
Phosphate Beneficiation
Market Specifications
Bone phosphate of lime, 70 to 72 per cent, common.
Bone phosphate of lime 72 to 77 per cent, premium.
Production Problems
Phosphate rock being a low-priced material is produced as near the fertilizer market as possible and haulage costs determine production. Flotation of fine sand from the pebble mines in Florida is economical because the material has been mined and presents a disposal problem if not salvaged.
Thorough desliming at 150 mesh is essential for best results by flotation. Large tonnages must be handled and flotation reagent costs must be low to make the process economical.
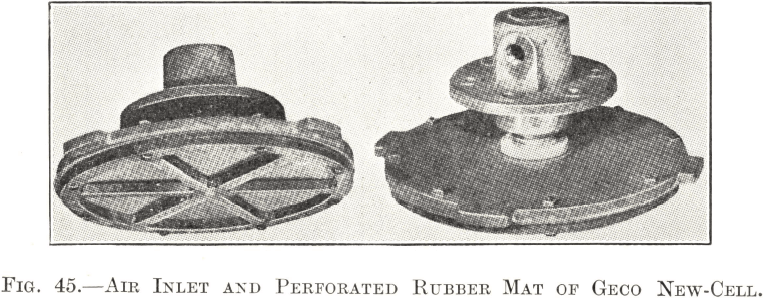
Reagent Combinations
Generally a fatty-acid reagent combination is employed to float the phosphate from the silica to produce a grade of 70 to 72 per cent BPL. Reagents are caustic soda, fuel oil, and Tall oil added to the pulp and conditioned at high density, 70 to 75 per cent solids, before flotation. For producing premium grade phosphate, the fatty-acid-floated product is conditioned with sulphuric acid to neutralize and cut off the oil film, washed, repulped, and the silica floated with a cationic reagent such as amine acetate. Flotation is very rapid. It is very important to employ the proper high-density conditioning technique to bring about thorough activation and selectivity in both the fatty acid and cationic flotation steps.
Flow-sheet of a Florida phosphate plant recovering —35+150 mesh phosphate by flotation. De-sliming and conditioning at 65 to 70 percent solids with reagents is essential for proper separation by flotation.
Source: This article is a reproduction of an excerpt of “In the Public Domain” documents held in 911Metallurgy Corp’s private library.