Table of Contents
The Sink and Float separation process is part of what is also known as a Heavy Media Separation Process (HMS) and are commercial adaptations of the common laboratory procedure used for separating a mixture of two products having differentials in specific gravity by immersing the sample in a heavy liquid having a gravity intermediate to those of the products to be separated. The lighter fraction of the two is floated at the surface of the liquid while the heavier product sinks. The heavy liquids commonly employed are inorganic salt solutions, such as of zinc chloride, or organic liquids, such as halogenated hydrocarbons.
Many years ago it was discovered that suspensions of finely divided solids in water closely approached the properties of heavy liquids in sink and float practice. If the solid phase of the suspension is ground to suitable fineness and mixed with water in correct proportion, a medium is obtained that is stable or so slow settling that a substantially uniform specific gravity can be maintained from top to bottom of the bath. As a consequence, no rising currents of water are necessary to assist in the separation of sink from float, nor is it necessary to supply strong mechanical agitation to maintain the medium in suspension.
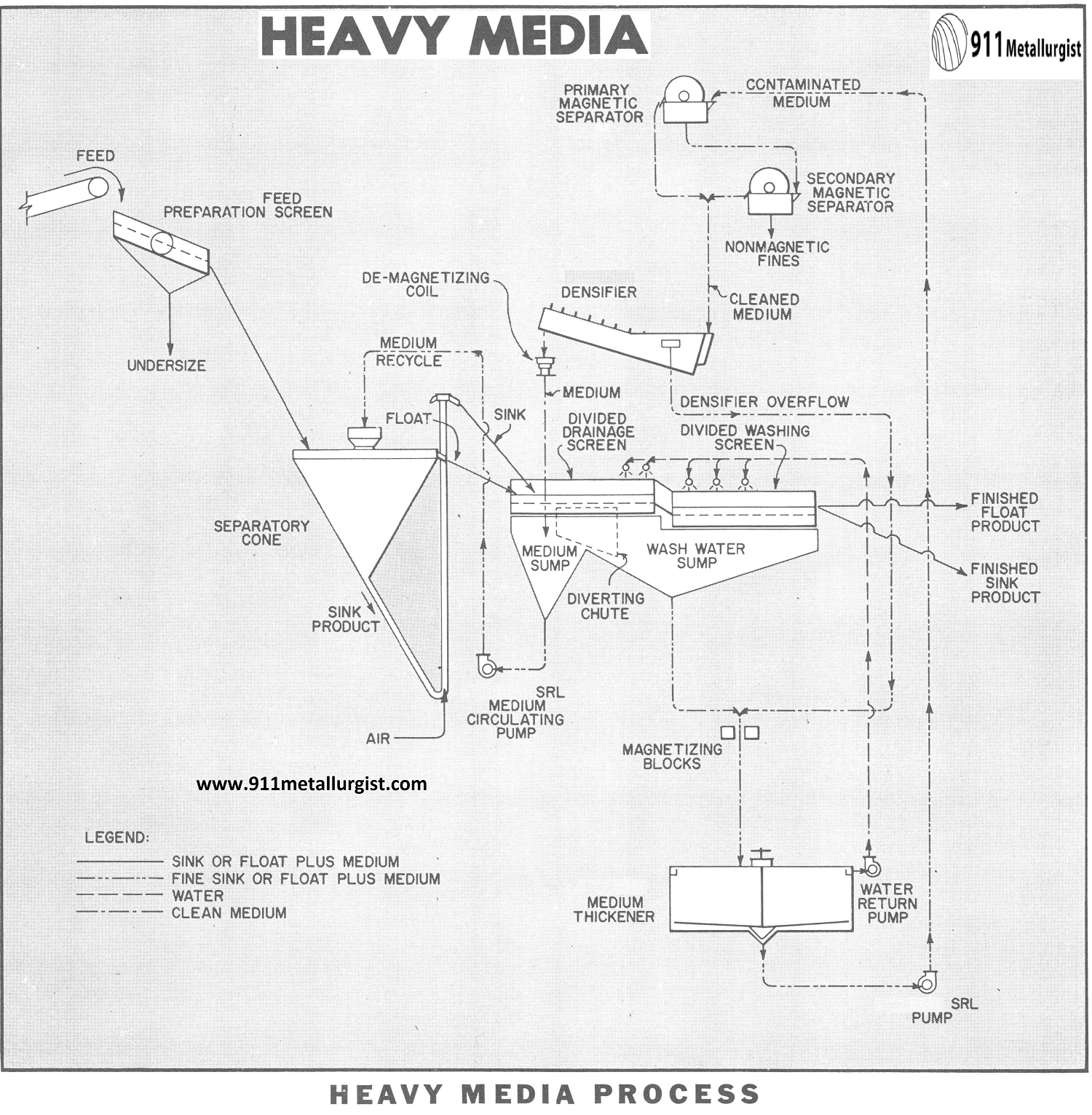
When materials are separated in such a suspension or medium, they will inevitably contain some contaminating fines or slimes resulting from incomplete washing of the feed material and from abraded fines generated through particle attrition as the material passes through the separating vessel. An accumulation of contaminating fines and slime in the bath would affect its specific gravity and viscosity and reduce its separating efficiency. Thus, in a continuous process it becomes necessary to provide means for continually cleaning a portion of the medium to eliminate slime at the same rate at which it is introduced into the medium by the incoming feed.
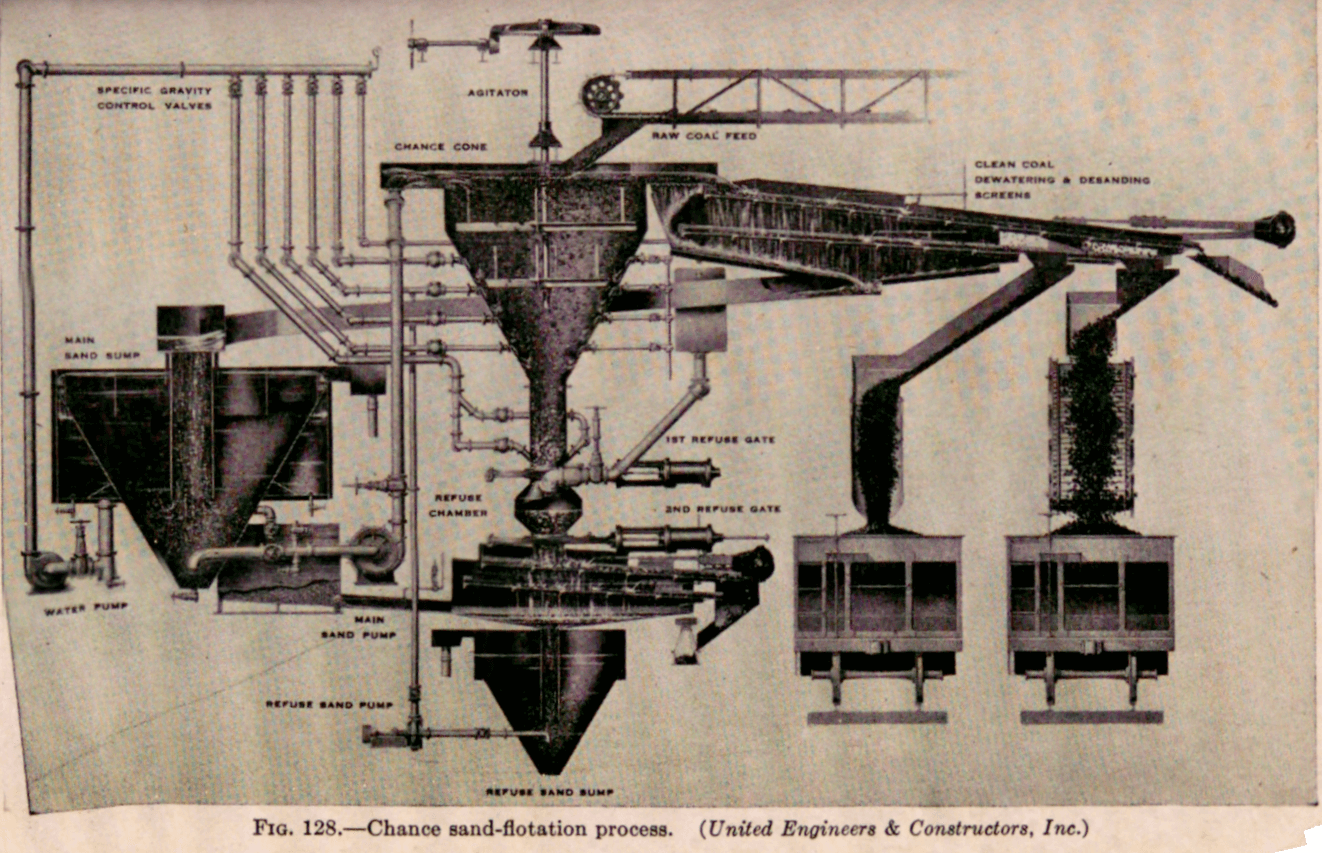
One of the first commercial applications of a medium to effect a sink-float separation used a fine silica sand suspension for treating anthracite coal and is known as the “Chance” process. The method used for cleaning the medium is decantation which limits the minimum grain size of the solid in the suspension. Any sand that is too fine is discarded, along with the contaminating slime, and since a coarse sand must be used to maintain a uniform suspension in the bath it is necessary to use strong rising currents. The combination results in a separation relying more on hindered settling classification than on sink-float principles.
There are other sink-float processes for cleaning coal less generally used, but similar to the Chance process. They employ other solids such as clay, barite, flue dust, etc., in the suspension. The medium is cleaned by decantation alone, or a combination of decantation and froth flotation for the removal of contaminating fine coal. The application of these various sink-float processes has been limited to the treatment of coals where the specific gravity of the required bath is less than 1.8.
The lead sulphide mineral, galena, is sometimes used in the sink-float treatment of certain lead-zinc ores. Froth flotation may be used for cleaning the medium or a portion of the medium can be continuously replaced with a fraction of the final galena concentrate being produced in the subsequent treatment of the ore.
The heavy-media separation process, or HMS, employing ferrous media, usually ferrosilicon and/or magnetite, is the most generally used process for sink-float separations. A stable medium over the range of specific gravities from 1.25 to 3.40 can be maintained within close limits and is cleaned and recovered by magnetic means.
The video here below feeds 2.5% Zinc into a Chance HMS Process to sink >10% Zinc rock and float 0.2% Zinc waste rock.
The >10% Zinc sunk, will become ball mill feed.
The HMS Heavy Media Separation Process Flowsheet
FEED PREPARATION SCREEN
The heavy-media feed, crushed to the proper size, is screened, washed and drained on the Vibrating Screen to eliminate as much of the fines as possible. The fines removed will usually range from ¼” to 10-mesh and be reserved for separate processing by gravity or flotation methods.
HMS SEPARATION VESSEL
The screened feed is fed to the separatory vessel which contains a suspension of finely ground ferro-silicon and/or magnetite in water, maintained at a predetermined specific gravity. The light fraction floats and is continuously removed by overflowing a weir. The heavy particles sink and are continuously removed by an airlift.
DRAINAGE SCREEN
The float weir overflow and sink airlift discharge go to a longitudinally divided drainage screen. On the drainage section more than 90% of the medium carried with the float and sink drains through the screen and is returned to the separatory vessel by the SRL Medium Circulating Pump.
WASHING SCREEN
The float and sink products pass from the drainage section of the screen to the washing section where substantially complete removal of adhering medium and fines is accomplished by water sprays.
MEDIUM THICKENER
The undersize from the washing screen, consisting of medium, wash water, and fine, too dilute and contaminated to be returned directly as medium to the separatory vessel passes through magnetizing blocks to the Medium Thickener. The thickener overflow is returned by the water return pump and reused as wash water. The medium particles of magnetite or ferrosilicon are magnetized by the blocks causing their flocculation and a greatly increased settling rate so that a smaller thickener is used.
MAGNETIC SEPARATORS
The SRL Pump elevates the thickener underflow to the primary and secondary magnetic separators operated in series. The tailing or reject from the secondary magnetic separator may go to waste or join the undersize of the feed preparation screen for treatment by some other method.
HEAVY MEDIA DENSIFIER
The clean magnetite or ferrosilicon reclaimed by the magnetic separators, flows to the Densifier for water removal and storage. By raising or lowering the screw in the densifier, the amount of medium returned to the separatory vessel is controlled to give the desired separating gravity. The medium has been magnetized by the blocks and the magnetic separators and is in a thoroughly flocculated state. In order to destroy the magnetic charge on the particles, and allow them to disperse uniformly through the water, the medium being returned to the circuit from the densifier, flows through a demagnetizing coil.
The flowsheet in this study illustrates the separatory vessel as a cone with an outside airlift. There are a large number of other type vessels in use but the basic flowsheet is essentially as shown regardless of the type separatory vessel used.
Three product separations, such as final float and sink products plus a middling with intermediate gravity are not uncommon in HMS plants. This requires additional separatory vessel, drainage and dewatering screen and medium circulating pump to be added to the basic flowsheet shown.
The size range of feed products being treated by sink-float processes is as high as 12″ on the upper end and 28-mesh on the lower end. The average being 2″ to 5″ by 4 to 10-mesh.
A partial list of minerals, ores and other materials being treated by sink-float processes are:
- Andalusite
- Dolomite
- Magnesite
- Anthracite coal
- Fluorspar
- Manganese
- Barite
- Garnet
- Pyrite
- Bituminous coal
- Gravel
- Steel mill slag
- Brucite
- Iron ore
- Tin ore
- Chromite
- Lead ore
- Uranium ore
- Diamond ground
- Lead-zinc ore
- Zinc ore
HEAVY-FLUID SEPARATION
If a fluid is available whose specific gravity is intermediate between that of two solids which it is desired to separate, no simpler process could be desired than to suspend the mixed solids in the fluid, allow one to rise and the other to sink, and draw off separate products from top and bottom of the separating vessel. A typical example is the separation of wood chips from gravel or sand, using water as the medium.
Since all minerals are heavier than water, water is not suitable for the practice of “float-and-sink” separation. Some aqueous soluitions are available, however, whose specific gravity is sufficient to permit coal to “cream” while associated impurities sink. Organic liquids having a specific gravity well above 2.75 but under 3.5 are available. They can be used to reject, as a light layer, the common gangue minerals quartz and calcite, but they are relatively expensive. Liquids having a specific gravity over 3.5 are few and very expensive even for laboratory and research purposes.
Heavy pseudo liquids can be made by suspending solids in water, and these fluids can be used almost like true liquids, provided the particles to be separated are coarse in comparison to the size of the “medium” particles, provided the “medium” is thin enough not to acquire plastic properties, and provided the “medium” is agitated enough not to settle.
Pseudo liquids are very much cheaper than organic liquids of high specific gravity, so the practical disadvantage of fluid loss is not nearly so significant. On the other hand, the use of pseudo liquids is not so simple as that of high-specific gravity liquids.
Laboratory Use of Heavy Liquids. In the laboratory, heavy liquids are very useful for assessing the optimum separation obtainable by gravity concentration: by the use of a series of fluids of graduated specific gravities, a crushed solid can be separated into fractions whose specific gravity lies within narrow limits, as 1.40 and 1.45, or 2.75 and 2.85. In this way, locked particles are segregated from free particles and locked particles of different compositions are separated from each other.
The procedure has not been applied to extremely fine particles, but can readily be used for all sieve sizes and the coarsest .sub-sieve sizes. For example, 200-mesh quartz settles approximately 4 in. in water in 15 sec. In this case, the viscosity is about 0.01 poise, and the apparent specific gravity is 1.65. If separation to 0.01 unit in specific gravity is desired and if t he viscosity of the fluid is ten times as large as that of water (corresponding to the viscosity of a free-flowing oil), the settling time should be some 1,650 times as large, or about 7 hr. for 4 in. Because of its reduction in settling time, centrifuging permits an extension of the float-and-sink procedure to subsieve sizes.
One of the most useful heavy fluids is acetylene tetrabromide (or tetrabromethane) whose specific gravity is 2.96. This fluid can be diluted with carbon tetrachloride and give solutions of lower specific gravity down to 1.59, the specific gravity of carbon tetrachloride.
Another useful group of fluids of low specific gravity (for coal analysis) is aqueous solutions of zinc chloride and of calcium chloride.
For specific gravities higher than 2.96, the student is referred to the review by Sullivan and to other special works.
Figure 127 represents the results obtained by float-and-sink on one sample of coal. This figure is typical of the studies currently made on the washability of coal. Determinations were made of the ash content of specific gravity fractions averaging, respectively, 1.28, 1.30, 1.38, 1.50, 1.70. 1.90, and 2.20. These fractions were obtained by the use of heavy fluids; their relative weights were determined. From the specific gravities and cumulative weights, curve I (specific gravity vs. cumulative weight) was drawn.
From the ash content calculated on a cumulative basis and the cumulative weight percentage, curve II was drawn. Curve III records also the elementary or actual ash content of each fraction against cumulative weight.
Thus if a separation is made by float-and-sink testing at specific gravity 1.40, the raw coal (containing 16.0 per cent ash) yields clean coal weighing 78 per cent of the raw coal (point A curve I) and containing 8.6 per cent ash (point B on curve II). If gravity methods are used, such a separation is the most that can be expected of that coal without further comminution.
(Curves IV and IYa are designed to give a measure of the difficulty in separating the raw coal into cleaned coal and waste at any specific gravity. Thus if a leeway of 0.10 in specific gravity of individual particle is permissible at 1.40 specific gravity, about 67 per cent of the coal falls between 1.30 and 1.50 specific gravity (point C curve IV). This indicates extreme difficulty of practical separation at that specific gravity. If, on the other hand, separation is attempted at a specific gravity of 1.50, and a leeway of 0.10 is permissible, about 14 per cent.
INDUSTRIAL PROCESSES USING HEAVY LIQUIDS
Three processes have been proposed that use true heavy liquids; the Lessing process, the Bertrand process, and the Du Pont (Nagelvoort) process.
The Lessing and Bertrand processes clean coal in a solution of calcium chloride, and the Du Pont process uses organic liquids of high specific gravity.
Lessing Process
Calcium chloride solution having a specific gravity of approximately 1.4 is used for the separation, which takes place in a cylindrical tank 6 to 10 ft. in diameter with a conical bottom, the total height being nearly 30 ft. Raw coal freed of dust and fines is introduced near the center of the tank after mixing with the separating solution in a mixer. The cleaned coal rises to the top where it is removed by a chain scraper and delivered to draining towers. The slate and bone are lifted from the bottom by a bucket conveyor and dumped in draining towers. After draining, the coal and the slate are washed, the wash liquor returning to the supply of calcium chloride. Further washes are required to free the coal completely of chloride; these go to waste.
Some 320 liter of liquor is withdrawn from the separating tank by each metric ton of raw coal. The specific gravity of the liquor is dropped from 1.4 to about 1.2 by the wash water and the inherent moisture of the coal. This 320 liter of liquor, now increased to about 640 liter, is concentrated by evaporation to the original volume. The loss of calcium chloride liquor is of the order of 2 to 3 liter per ton of raw coal.
The Lessing process has been installed in Wales and has produced extremely clean coal; the clean coal is even freer of chloride than the raw coal. It would seem, however, that the cost of thermal concentration of the separating liquor will stand in the way of widespread adoption of the process.
Bertrand Process
The Bertrand or Ougree-Marihaye process also utilizes a calcium chloride solution as separating medium and is applicable only to deslimed feed. In practice, particles varying from 1 to 5 mm. in diameter are treated by this process in Belgium. It differs from the Lessing process in that the raw coal is introduced into the system countercurrent fashion, from water to separating solution, the purified coal and the waste being withdrawn in a similarly countercurrent fashion. There are five circulating liquors, viz., hot water, weak solution, medium solution, strong solution, and separating solution.
The Bertrand process avoids the costly thermal concentration of the diluted leach liquor, but introduces a relatively complex hydrometallurgical flow sheet.
The results obtained by these processes are excellent, coal of extremely high grade being obtained in amounts substantially in agreement with theoretical yields. Coal containing less than 1 per cent ash is said to be obtained by the Bertrand process. Coal of such purity is in demand for the manufacture of special electrode coke, for the preparation of colloidal coal, for hydrogenation, as fuel in Diesel engines of the Rupa type, and as fuel in automotive gas producers.
Du Pont Process. The Du Pont process, an outgrowth of the Nagelvoort process, is a practical adaptation of the laboratory heavy-liquid separation which has already been described. In basic principle, it does not differ from that laboratory procedure. But several requirements have had to be met in order for the process to become commercial. These are as follows:
-
- Low solubility of the “parting liquid” in water and of water in the parting liquid.
- Low viscosity (high fluidity) of the parting liquid at operating temperatures.
- Stability, low vapor pressure, and non-flammability of the parting liquid.
- Prior preparation of the ore to remove fine particles.
- Prior preparation of the ore with suitable chemicals to make the surface of the particles immune to wetting by the parting liquid.
- Complete sealing of the separating system to prevent loss of parting liquid by evaporation and to eliminate the health hazard due to the noxious vapors of the parting liquid.
- Use of a procedure that completely separates the parting liquid from the separated minerals, so as to completely regenerate the parting liquid.
- Use of a scheme for constantly purifying the parting liquid.
Of these various requirements, the most important was requirement 5, inasmuch as reasonable reagent consumption could not be expected if it were not met.
So-called “active agents” have been devised to keep the minerals wetted by water rather than by parting liquid. In the case of coal, the active agents are starch acetate or tannic acid. The concentration of active agent in water is of the order of 0.01 per cent.
The main expense in the Du Pont process is for the parting liquid, which is a mixture of several halogenated hydrocarbons. The consumption of medium is said to be very low, and often well under 1 lb. per ton of coal treated.
Clearly the separating process although simple in principle requires a number of adjunct operations for the sake of economy in reagents and from a physiological standpoint. The process is not applicable to fine particles. It is therefore limited to the treatment of minerals in a coarse state of subdivision, and such a treatment cannot be expected to be successful unless the ore is coarsely aggregated or if low standards are permissible.
Amber is separated from associated impurities by the use of heavy liquids.
INDUSTRIAL PROCESSES USING HEAVY SUSPENSIONS
Industrial processes using heavy suspensions have behind them the record of many years’ practice in the washing of coal, but their application to ores in which a separation is to be made at a specific gravity of over 2.6 is still very recent.
These processes include the Chance sand-flotation process, the Vooys barite-and-clay process, and the Wuensch process.
Chance Process
For cleaning coal, the Chance process has been in use for about 20 years. The medium consists of a suspension of sand in water. The sand must be of relatively uniform size, — 40 + 80-mesh being preferred. Coarse sand tends to accumulate in the bottom of the separating vessel, and fine sand is harder to retrieve, as well as likely to accumulate in the upper stratum of the separator.
The Chance cleaner (Fig. 128) consists of a separating vessel (cone separator) in which the sand suspension moves gently upward. An agitator, by stirring the suspension, prevents packing. The overflow of clean coal and sand passes over clean-coal screens which desand and dewater the coal, spray water being used for desanding. The underflow of the separator passes through refuse valves (two of these valves enclosing a refuse chamber are used to provide a water seal) on refuse screens. These work like the coal screens to desand the refuse. The diluted sand, including sludge coal, is purified in a cone thickener, the sludge coal being wasted. The regenerated medium is returned to the system with new feed.
The specific gravity of the fluid mass is adjusted by varying the proportions of sand and water.
For the cleaning of anthracite, a heavier specific gravity must be maintained in the suspension than is necessary for the cleaning of bituminous coal.
Vooys Process
In the Vooys process, the suspension consists of clay and finely ground barite (—150 or —200 mesh) in water. As the process is applied at the Sophia Jacoba mine (Holland), the specific gravity is adjusted at 1.47 and in so far as possible, particles of raw coal finer than 100-mesh are excluded.
Since the solids in the medium are much finer than in the Chance process, the coal that can be treated can also be much finer. This perhaps explains why a coal containing as little as 3.3 to 3.4 per cent ash is steadily produced, with a yield practically equal to the theoretical float-and-sink yield.
Regeneration of the medium requires the use of a thickener; the loss of barite is of the order of 2 lb. per ton of raw coal. The operating cost for the whole plant is given by Berthelot as 1.13 francs per metric ton, or approximately 3 cts. per short ton of raw coal on the basis of treatment of 150 tons per hr. The cost seems lower than for a corresponding jig plant, and the results are better.
Source: This Sink and Float separation process article is a reproduction of an excerpt of “In the Public Domain” documents held in 911Metallurgy Corp’s private library.