Table of Contents
Hydrometallurgical methods have received increased attention for the treatment of many ores in recent years. Whereas, direct furnacing has been regarded as the standard process for mercury (cinnabar) ores, hydrometallurgical methods offer an alternate consideration. The chemistry of this process is not new, but with the impetus to hydrometallurgical methods, it is only logical that this method should receive increased attention. The process parallels cyanidation for the recovery of gold and silver in many ways. The mercury sulfide (cinnabar) is dissolved in a sodium sulfide-sodium hydroxide solution and washed from the solids using counter-current decantation. The mercury is precipitated from solution using metallic aluminum.
An important contribution to the advancement of leaching practices for mercury ores is Report 5 entitled “Studies in the Hydrometallurgy of Mercury Sulfide Ores” by John N. Butler and published by the Nevada Bureau of Mines, Reno, Nevada. This report, here below, is an excellent reference.
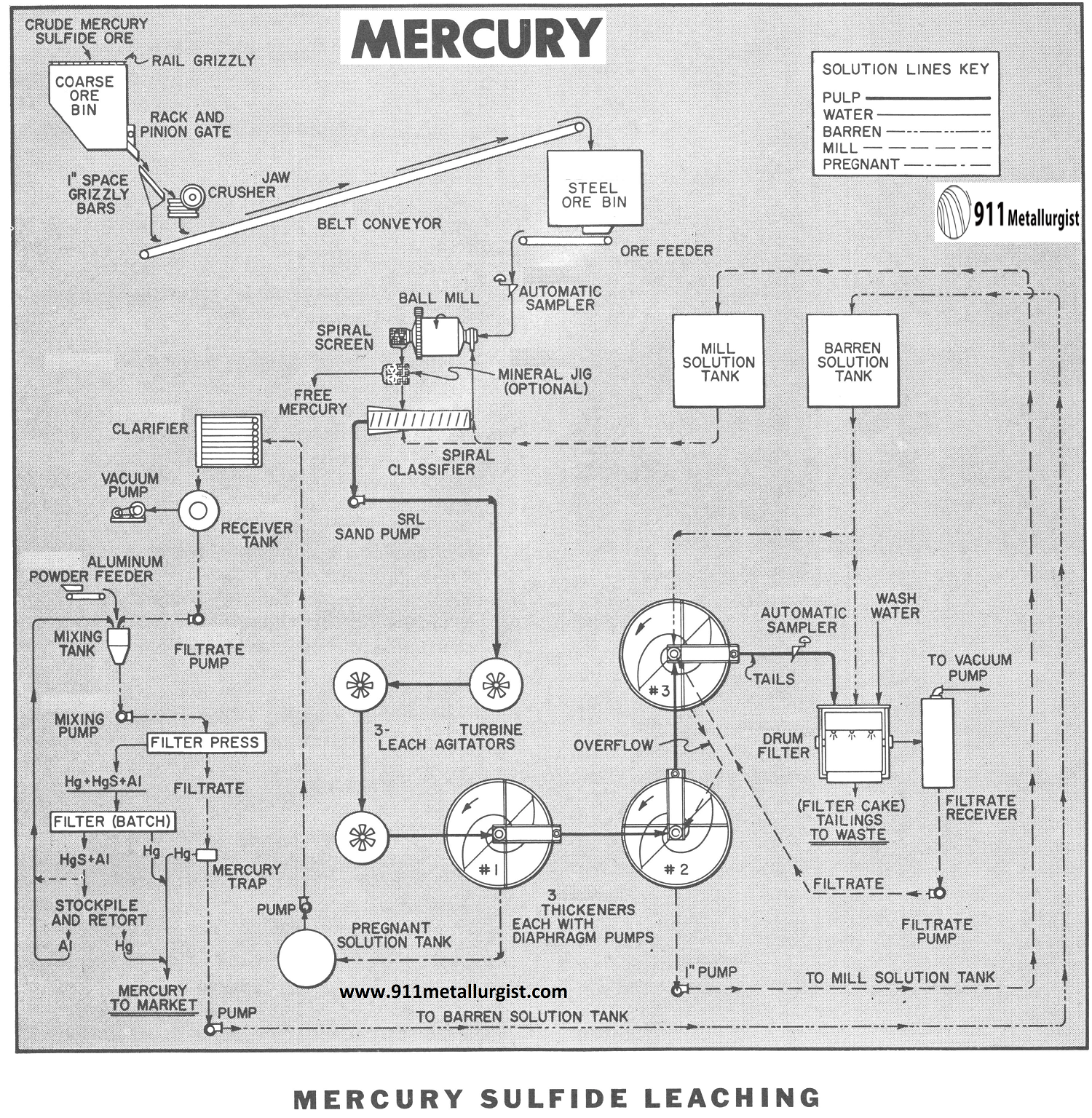
The flowsheet in this study represents a condensed presentation of the process and is intended only to illustrate the general features of the treatment steps. Extensive testing should precede any plant installation.
The Mercury Leaching Process Flowsheet
CRUSHING – GRINDING – LEACHING Mercury Ore
The first part of the flowsheet consists of conventional single stage crushing which is typical of most small capacity plants. Crushing is usually performed on an eight hour period at a rate to provide sufficient crushed ore in storage to operate the balance of the plant “around the clock.”
Grinding to minus 65-mesh using a Ball Mill in closed circuit with a Spiral Classifier or Cyclone liberates the cinnabar (mercury sulfide) from the associated gangue and exposes it to the dissolving action of the leach solution containing 1% sodium hydroxide and 4% sodium sulfide. Considerable dissolution of the mercury sulfide is accomplished in the grinding circuit, but about four hours retention time at 33% solids in leach agitators will insure optimum extraction. Turbine Type Agitators are widely used in hydrometallurgical plants due to their ability to maintain solids in suspension with low power.
The basic chemical reaction for dissolution of cinnabar is as follows:
HgS + Na2S = HgS . Na2S (solution)
Sodium hydroxide is necessary in the above reaction to prevent hydrolysis of the sodium sulfide. The soluble sulfide, HgS.Na2S, is relatively unstable, any sudden decrease in the concentration of free sodium sulfide in the leach solution will cause the precipitation of black mercury sulfide. Precautions are therefore necessary to prevent dilution of the solution with water or by other reactions which may lower the free sodium sulfide concentration of the leach liquor.
Metallic mercury is not soluble under these conditions and, if present, is recovered by the Mineral Jig in the ball mill-classifier circuit.
COUNTER-CURRENT DECANTATION
The pregnant solution is separated from the solids using three Thickeners arranged for counter – current decantation followed by final filtration on a drum filter. Small amounts of barren solution and approximately ¼-ton of water per ton of ore are used for washing the filter cake. Barren solution is added to the feed well of the No. 3 thickener and overflowed to No. 2 thickener. The overflow from the No. 2 thickener constitutes the mill solution for use in the grinding circuit. The pregnant solution is removed from the No. 1 thickener.
The addition of a flocculant is necessary to increase the settling rate and produce a clear, supernatant liquor in the thickener.
Precipitation—The reaction for the precipitation of the mercury from solution is as follows: 3(HgS.Na2S)+8Na0H+2Al=3Hg+6Na2S+2NaAlO2+4H2O
Liquid mercury metal, mercury amalgamated with aluminum, and black mercury sulfide are formed during precipitation. High efficiencies are obtained in precipitation and sodium sulfide is regenerated for recycle. Sodium hydroxide and aluminum are consumed during precipitation.
Various schemes for precipitation with metallic aluminum are possible, however, continuous systems similar to the procedure employed for precipitation of gold and silver from cyanide (except using powdered aluminum instead of zinc dust) afford a simple and efficient method. Since the precipitated mercury is liquid and will pass through the filter press with the barren solution, it must be collected in a mercury trap ahead of the barren solution tank. Excess aluminum powder in amalgamated form and a small amount of mercury sulfide will accumulate in the filter press and can be retorted periodically or returned to the precipitation circuit.
CHEMICAL CONSUMPTION
As in any hydrometallurgical process, the consumption of chemicals will vary depending on the ore characteristics. The summary lists typical consumption figures as a general guide.
Source: This article is a reproduction of an excerpt of “In the Public Domain” documents held in 911Metallurgy Corp’s private library.