Table of Contents
Potash occurs in soft deposits generally associated with sodium chloride and varying amounts of clay slime, which because of its colloidal character, complicates the beneficiation process.
Potash ores generally contain 20 to 40 percent KCL with the balance being NaCl and a small amount of clay slime, the latter usually in the order of 1 to 1½%.
Flotation has been developed as the principal separating process for the potash salts which generally are coarsely crystalline and free from the sodium salts at about 10 to 14 mesh. In most cases the potash is floated in the froth product and the salt, NaCl, discarded as tailings. A plus 60% K2O product is required and flotation normally will maintain grade at 61 to 62% K2O without difficulty provided thorough desliming is accomplished in the classification.
The potash processing flowsheet
In this case the potash mineral, sylvite (KCl), is floated from the sodium chloride, Halite (NaCl).
Common Salt or Halite: NaCl
Common Salt or Halite: NaCl is Colorless when not stained with some impurity; luster, glassy; H = 2.5; G = 2.14; crystals, in cubic system, cleavage, perfect, cleavage pieces with square edges and corners; well-known taste; composition, sodium chloride, a combination of the metal, sodium, with the gas, chlorine. Domestic and preservative uses are well known; large quantities are used in the manufacture of sodium, chlorine, washing soda, baking soda, caustic soda, etc. Found in large quantities in sedimentary rocks of many ages, with gypsum, shale, sandstone, and limestone. It is mined as rock salt. Its presence in sea water, salt springs, and salt lakes is well known.
Crushing Section
The mixed salts are usually mined from underground workings and are thoroughly dry. Three stage crushing, with Jaw Crushers and Rolls and hammer mills is provided which will reduce the mine run ore to minus 6 mesh with a minimum amount of fines. Finished material is screened out between each crushing stage and the oversize from the third stage is re-cycled or in closed circuit.
The soft and only slightly abrasive character of the salts makes dry crushing relatively simple, although provisions must be made for dust control. Hammer mills can generally be set to dry crush to 95% — 10M.
Scrubbing and Desliming
The dry crushed ore at minus 6 mesh is fed into a rotary drum scrubber with saturated salt brine. The action in the scrubber scours off the surface film of clay slime from the salt crystals. The slurry discharging from the scrubber is deslimed in a Classifier set to overflow at about 28 mesh. Brine wash is used on the salt bed in the classifier to remove as much of the primary slimes as possible. The classifier overflow is further deslimed in a Hydroclassifier to reject the true colloidal slime and recover the fine crystalline salt for flotation feed.
Grinding and Classification
The deslimed classifier coarse salt product is ground in a Rod Mill in open circuit to approximately all minus 14 mesh. The rod mill discharge flows to a second classifier for desliming in the same manner as in the classifier after the scrubber. In case a finer grind is desired the rake product may be in closed circuit with the mill. Open circuit is usually satisfactory, since it does remove a big bulk of the load from the subsequent classification and thickening stages, and also provides a higher solids feed for conditioning and flotation.
Conditioning
The deslimed ground and classified salts at approximately 60% solids (about 54% brine by volume) are conditioned in open type Conditioners using rubber covered turbine type propellers. Generally in the first conditioner a reagent such as starch or Guartec may be added to neutralize and depress any slime not removed in the classification steps or formed by subsequent abrasive action of the pulp. In the second conditioner one of the aliphatic amine acetates is added to activate the sylvite and render it floatable. The salt sodium chloride is not effected and remains wetted. A frother such as pine oil is usually added for froth control.
Potash Flotation
The conditioner and reagentized salt-brine slurry is floated in a “Sub-A” Flotation Machine. In the circuit shown, roughing is accomplished in a “Sub-A” Free Flow Flotation Machine with no intermediate weirs or feed pipes. This allows the coarse sodium chloride waste product to flow through the machine unmolested. Flotation is generally very rapid if the feed is properly conditioned. Usually 1.5 to 2.0 minutes will be sufficient, but an adequate factor of safety is provided for fluctuations—feed rate and grade. Flotation density is maintained at 25 to 30% solids at the feed end of the machine.
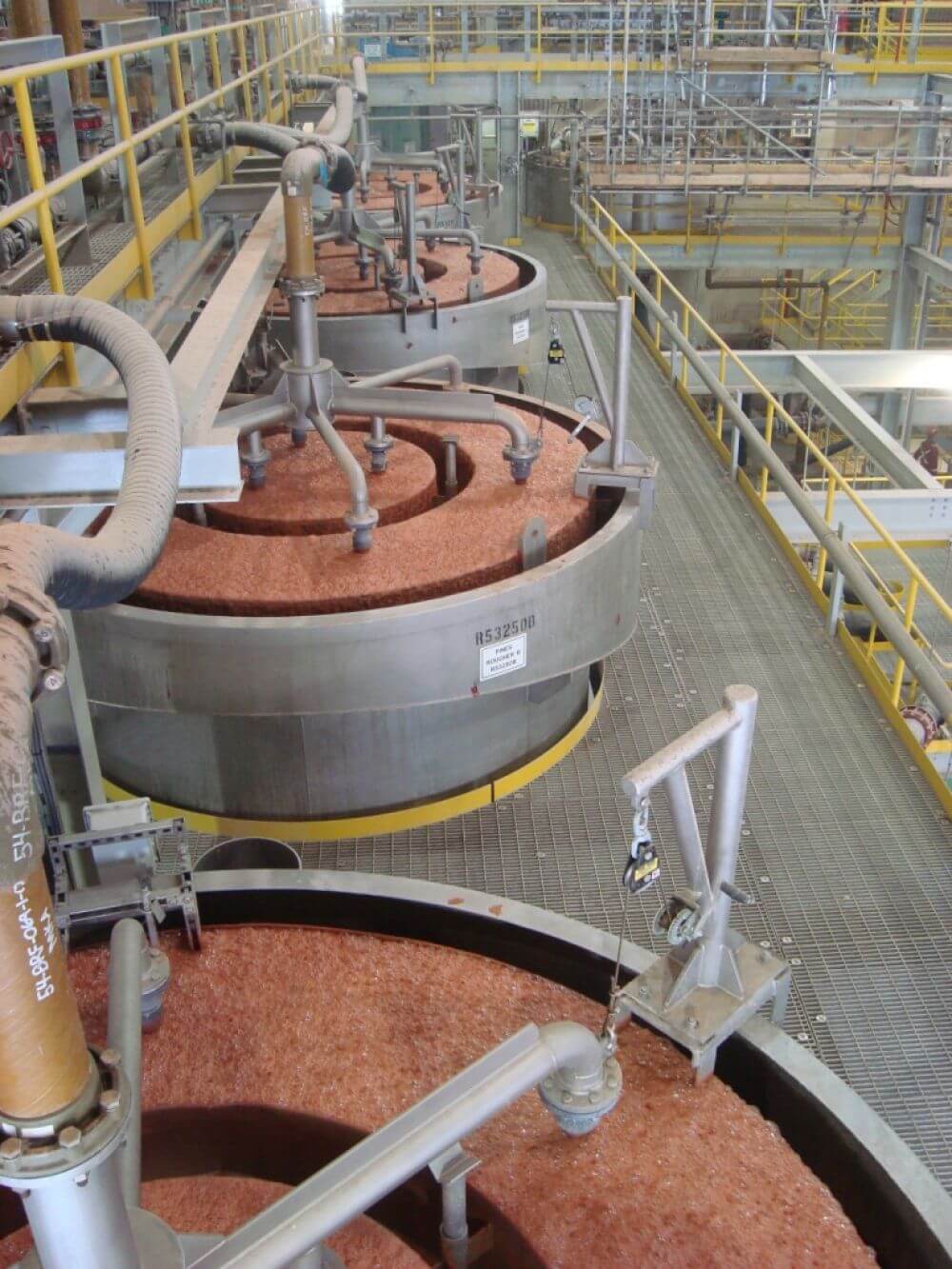
Rougher froth concentrates are cleaned once in a “Sub-A” Cell to Cell Flotation Machine. Cleaner tailings are returned to the roughers by gravity. Generally because of the large volume of froth concentrate to be removed in the roughers and cleaners a double overflow machine is used. For simplicity a single overflow machine is shown in the flowsheet.
“Sub-A” Flotation Machines will effectively produce high grade concentrates and low final tailings, or properly ground, deslimed, and reagentized potash feed. For very coarse solids it may be advisable to provide a separate circuit for the coarse fraction. In one case Cells are effectively floating —6 + 15 mesh potash and producing a plus 61% K2O products with a high recovery. In some special circuits, the cleaner tails are screened and the —28 mesh discarded to waste. The +28 mesh may be retreated by further grinding or combined directly with the finished potash product, provided the overall grade can be maintained at +60% K2O. Final flotation tailings will generally contain 0.5 to 0.9% K2O, thus giving about 95% recovery in finished concentrate form.
Thickening, Filtering and Brine Recovery
The froth product from the cleaner cells is conditioned to break down any froth and the excess bi-passed to a thickener for brine recovery. The thickener underflow is recycled to the conditioner for bringing up the density in the filter feed. Filtrate from the filter is recycled to the thickener. Fresh water wash may be used on the filter cake to remove the brine still high in NaCl content.
Filtering is accomplished in a top feed filter because of its fast settling free-filtering characteristics. Horizontal pan type filters and centrifuges also have application in the handling of potash salts. Drying is accomplished in rotary dryers, either oil or gas fired.
Conditioning and two or more stages of thickening is employed for brine recovery and rejection of the coarse crystalline salt and colloidal slimes as separate products, each with a minimum loss of potash salt or solution.
Pumping of Products
SRL Pumps are used effectively for handling brine pulps. Adjustable Stroke Diaphragm Pumps are standard for removing the underflow pulps from the thickeners and hydro-classifiers. The pumps are field proven and several hundred are used in the various potash plants in the U.S., France and Mediterranean areas.
Sampling
Automatic Samplers with both wet and dry type cutters are very effective in quality and metallurgical control in the potash plants. Samplers are shown at the essential places, on the flowsheet.
Summary of the potash process flow diagram
Flotation of potash has been developed to a highly successful degree. It has greatly simplified the processing of the salts even in cases where the composition deviates considerably from the simple KCl-NaCl mixture. Special techniques in reagents and temperature control and even refrigeration are all factors in the processing of these salts. “Sub-A” Flotation is an important part in the processing because of its selectivity, flexibility, and ability to handle high tonnage as well as coarse sizes. It is the heart of the process, yet represents only a very small fraction of the initial equipment cost.
In some cases it is preferable to use a belt conveyor instead of a bucket elevator.
Potash Beneficiation
Potash Market Specifications
K2O………………………………………………………………………………….60.0 per cent
KCl…………………………………………………………………………………..95.0 per cent
Chemical manufacture grade KCl demands less than 1 per cent total impurities.
Production Problems
The flotation separation of KCl from NaCl or vice versa is no serious problem. Occasionally, in some European countries, considerable clay slime occurs in the deposits which causes difficulty in separation of the slimes from the brine circuits. De-sliming ahead of conditioning and flotation is important when floating the potassium chloride from sodium chloride.
Reagents
For floating potash from sodium chloride in a saturated brine solution it is necessary to de-slime and treat the pulp with starch or guartec. Cationic reagents such as amine acetate then will activate and selectively float the potash from the impurities. Anionic flotation with naphthenic acid and metal salts such as lead chloride is also practised to float the sodium chloride from the potash. In general, cationic reagents are preferred as they coat the floated potash and simplify subsequent handling after filtering and drying. The amine-coated particles, when dry, show less tendency to cake or cement in storage.
Source: This article is a reproduction of an excerpt of “In the Public Domain” documents held in 911Metallurgy Corp’s private library.