Table of Contents
- Froth Flotation Method for Sulphide Ores
- Oxide Flotation
- Flotation of Industrial Minerals
- Fluorspar Flotation
- Talc Flotation
- Phosphate Flotation
- Manganese Flotation
- Mica Flotation
- Tungsten Flotation
- Coal Flotation
- Feldspar Flotation
- Clay Flotation
- Silica Sand (Quartz) Flotation
- Cryolite Flotation
- Graphite Flotation
- Bauxite Flotation
- Magnesite Flotation
- Iron Ore Flotation
- Titanium Flotation
- Barite Flotation
- Spodumene Flotation
- Sulphur Flotation
- Nepheline Syenite Flotation
- Salt Flotation
- Potash Flotation
- Cement, Limestone and Flotation
- Miscellaneous Non-Metallics Flotation
- Industrial Flotation
The Froth Flotation Machine is universally used for all types of flotation problems. This machine finds a wide acceptance due to its flexibility in construction, which allows the machine to be adjusted to handle pulps with divergent physical characteristics, as well as the common and intricate metallurgical problems which confront the present day operator.
The Froth Flotation Machine is so designed that it will do a most acceptable job for coarse as well as fine flotation. The selectivity and flexibility are outstanding features and these, coupled with low operating and maintenance costs, makes the “Sub-A” synonymous with the word FLOTATION.
The tool “Floatation” since its general introduction some thirty years ago, has made rapid strides until it is now used for concentrating more ores than any other process. The “Sub-A” itself came into being in 1927 and in the intervening years its development has kept pace with the advancing technique in the ever-widening field of ore dressing. Flotation and the “Sub-A” are now major factors in the concentration of:
- Free metal ores;
- Sulphide ores;
- Metallic oxides;
- Non-sulphide or non-metallic ores, and in addition, progress is being made with
- Industrial applications.
The following resume gives a brief insight into the wide field of application under the five general headings just outlined.
Flotation of Free Metal Ores
Flotation is not generally applied to ores containing a preponderance of values in free metals except for certain well-known exceptions such as the floating of native copper, gold, silver, and free metals having a high degree of luster.
Native Copper Flotation
The notable occurrence of native copper ores is in the Keewenaw district of Northern Michigan. This area, one of the older mining districts of the United States, obtained its recovery entirely with gravity plants until the late 20s. As higher recoveries became more essential, a detailed investigation was made of the flotation process and it was put into general use immediately thereafter for the recovery of relatively fine native copper, heretofore lost in the gravity plants.
“Sub-A’s” were used for the early test work and since then have been extensively used for recovery of native copper by flotation. Today they are handling a predominance of the tonnage by this process. “Sub-A’s” have been eminently successful on this work due to their ability to handle coarse feed by the gravity flow method of concentration and to make an exceptionally high ratio of concentration.
Another innovation in copper recovery is the recovery of a precipitated metallic copper in a highly acidic circuit by Flotation, LPF, in a Utah plant.
Native Gold and Native Silver Flotation
While the occurrence of ores with their values as free gold and silver is very extensive, floatation is not at present as widely used as it should be. In most cases recovery and extraction of free gold and silver is by means of amalgamation, gravity, or cyanidation or a combination of these methods. However, flotation is sometimes necessary where certain physical conditions preclude the use of other processes. Notable examples are in extremely slow settling ores, as well as ores containing excessive cyanicides or soluble salts detrimental to amalgamation.
In recent years there has been a trend toward decreasing plant and operating capital cost but not sacrificing net return, by employing a combination of flotation and gravity with cyanidation of the concentrates. This type flowsheet has been a most important advancement. Its successful application is indicated by many operating plants in Canada, USA, Philippines and other sections of the world.
Generally, the flowsheet just described depends on gravity (usually jigs in the grinding circuit) or by coarse flotation in Flash Flotation Cells for recovery of the free and coarse precious minerals. Flotation on the classifier overflow is used to produce a final tailing and a high ratio concentrate for subsequent amalgamation and/or cyanide treatment.
Froth Flotation Method for Sulphide Ores
The floatation process at present finds its greatest scope in recovery from ores whose predominant values are associated both chemically and physically with sulphides. The major proportion of the present day world’s base metal production is procured by the flotation process. Since its inception flotation has been responsible for a vast improvement in the metallurgy of sulphide ores. Previous to concentration by flotation, gravity methods were used almost entirely to produce a concentrate for subsequent treatment. While this method produced fairly acceptable grades, the recoveries were generally far from satisfactory. Furthermore, it was impossible to control the constituents of the product as far as overall analysis was concerned. Partial success for ultimate analytical control was obtained by the use of such devices as magnetic separators, intricate gravity separations which were low in capacity, and close control of the feed entering the concentrators. This latter resulted in economic waste. This type of treatment was generally inefficient as very close supervision was required, dilutions were high, and the resultant low capacity, coupled with large floor space requirements and high capital costs, precluded the treatment of ores which now can be handled with a substantial margin of profit.
The adaptation of flotation to the treatment of sulphide ores was a major step in the advancement of concentration technique. This process, coupled at times with some gravity and improvements in equipment efficiency, enabled the characteristics of concentrates to be steadily improved and ore reserves were greatly enlarged due to the consequent lowering of costs. These improvements have taken place over many years and there is every likelihood that further advancements will be obtained as time progresses.
The use of flotation for sulphide concentration has meant a remarkable improvement in grade and the selectivity of this process has resulted in the rejection of undesirable constituents. It is now possible by using the correct flotation machine to make a product which will realize to the producer a high economic return. No longer are the smelters and other purchasers of concentrator products required to accept inferior feed for their respective plants, as a properly equipped milling plant could satisfy the rigid demands of the purchaser.
The “Sub-A” Flotation Machine has been and continues to be a major producer of sulphide, particularly base metal concentrates. The exclusive features of this machine pay dividends in metallurgical efficiency. A brief reference review of its general use in the following fields indicates the wide acceptance of the “Sub-A”.
Copper Floatation
Froth Flotation Cells are a big factor in the production of copper concentrates in various sections of the world. They are extensively used for producing a high-grade copper-sulphide concentrate low in iron. They are widely used in Canada (British Columbia, Manitoba, Ontario and Quebec), United States (Tennessee, Nevada, Utah, Colorado, Montana, Idaho, California, New Mexico, Arizona), Mexico, Chile, Peru, Ecuador, Bolivia, Cyprus, Newfoundland, Rhodesia, Belgian Congo, Philippines, Russia, Europe and many other localities.
Some of the larger copper producers have found the supercharged Flotation Machine eminently satisfactory for handling high tonnages through individual machines giving grade, recovery, and low cost.
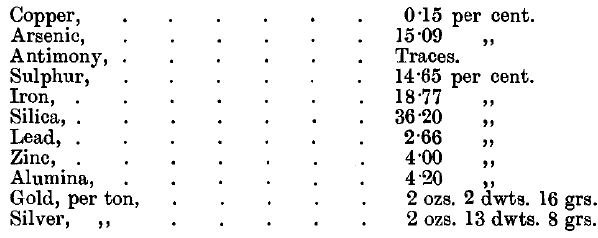
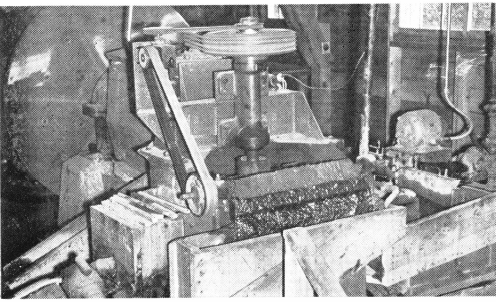
Lead Flotation
As selectivity is important in the production of lead concentrates, “Sub-A’s” are consequently quite extensively used. It is usually necessary to have two or more cleaning stages in a lead circuit and this is achieved on the without the use of pumps, brought about by the gravity flow principle.
Lead concentrates are produced on in such widespread localities as Australia, Argentina, Canada, United States, Mexico, Morocco, and before World War II in Burma, Poland, Yugoslavia and several localities in East Asia. There are several sections where small producers are operating and these augment the major production just outlined.
Flotation and “Sub-A” have played a major part in lead metallurgy as by its use separations are now achieved which were formerly considered impossible. The Unit Cell and the Mineral Jig operating in the closed grinding circuit are most often a valuable tool for producing a high grade concentrate valuable for subsequent dewatering and smelting.
Zinc Flotation
In the production of zinc concentrates by flotation the important factor is the rejection of iron in the form of iron sulphides. Here again, selectivity and grade are essential and with several cleaning cycles usually required, “Sub-A’s” consequently play a most important part in world zinc production.
Zinc concentrates are produced commercially on the several sizes of “Sub-A’s” and tonnages to individual machines vary from a few tons to well over 2500 tons per 24 hours. As the use of these machines is widespread the geographical list would thus be considerable. The supercharged No. 30 are used in Manitoba, Quebec, Colorado, Montana, Illinois, Wisconsin and Africa. The list of No. 24 installations producing zinc is large. These machines are operated both as the standard and supercharged type and are widely used for roughing and cleaning in the United States, Canada, and Mexico, as well as Newfoundland, Poland, Yugoslavia, Russia, Burma, etc. The Supercharged Machine is a popular machine in Canada where it is giving very acceptable results.
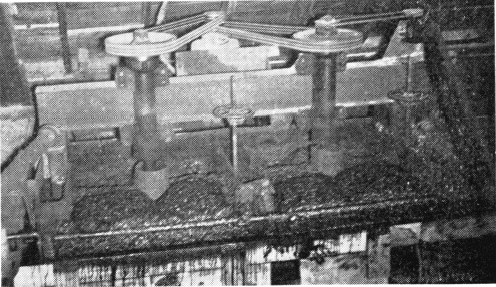
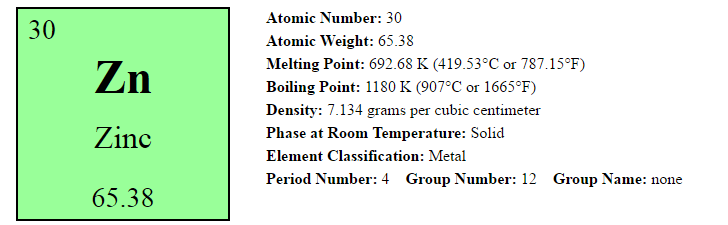
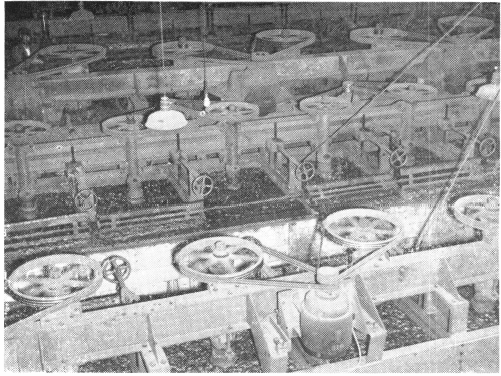
For smaller tonnage plants the smaller sizes of machines are used in various sections of the world. Usually a large number of zinc cells are used to give the necessary roughing, cleaning and re-cleaning steps.
Nickel Flotation
The problem in flotation of nickel sulphide ores is the high selectivity required for a high ratio. Mechanically the flotation cells are required to handle a coarse high density feed which in itself presents a difficult operating condition. “Sub-A” Flotation Cells are used quite extensively for flotation of a copper-nickel concentrate as well as a nickel concentrate following a copper circuit. Flotation Machines are used for production of concentrates for nickel smelting and with their special wear qualities are giving good service under these rigorous conditions.
Molybdenum Flotation
The flotation of molybdenite requires multi-stage cleaning to produce the necessary high- grade concentrate required. A considerable proportion of “Moly” production is acquired as a by-product from copper concentration plants. “Sub-A’s” are frequently used in these circuits as the several cleaning steps (4-8) can be completed in one machine without resorting to the use of pumps for recirculation of middling products.
Flotation Machine is a valuable unit for the last cleaning stages due to its identical construction to the larger rougher and cleaner machines. The use of the Unit Cell in the grinding circuit is most valuable in the recovery of this mineral.
Mercury Flotation
The flotation of mercury ores containing cinnabar, livingstonite, and meta-cinnabarite is being successfully accomplished in Mexico and Chile. Test work indicates flotation is very practical for recovery of mercury from ores from several parts of the world.
Mercury flotation is relatively simple and in general a very high ratio with high recovery is easily obtained. The use of flotation to produce a high- grade concentrate is the big factor, when used in conjunction with roasting, in saving on capital cost. Instead of roasting large tonnages of ore, this roasting section of the plant, when handling flotation concentrates for production of metallic mercury, can be small or even on a batch basis.
Antimony Flotation
Antimony in its sulphide form, stibnite, is relatively easy to recover by flotation. However, plant installations are not numerous. Perhaps the chief problem in flotation of antimony ores is the fact that they are frequently associated with arsenopyrite and due to dense texture it is often difficult to make a satisfactory separation. A further problem is the fact that antimony minerals slime readily, but this metallurgical problem can be overcome by the use of a Unit Cell in the grinding circuit.
Flotation on antimony ore has been successfully accomplished with “Sub-A’s” in Idaho, Nevada, Canada, India, Madagascar and in several other localities.
Pyrite and Pyrrhotite Flotation
These two minerals are being recovered by flotation for sulphur content as well as gold. In both instances high-grade concentrates are desirable to minimize subsequent treatment. Usually pyrite or pyrrhotite for sulphur is recovered as a by-product in which case the nature of the pulp is average; however, there are several instances where this is not the case. Sometimes the feed is very coarse or an acid circuit is required and in either case this presents a specific pulp handling- problem. The recovery of pyrite or pyrrhotite by flotation for gold content and sometimes as a smelter flux is very widespread and in this service Sub-A’s” can be found in practically every mining locality. They are also widely used wherever pyrite and pyrrhotite are recovered for their sulphur content, especially in Canada and the United States. Copper sulphate and caustic soda are often beneficial in flotation.
Arsenic Flotation
Arsenic is usually recovered as a by-product from auriferous arsenopyrite ores, either by roasting or smelting flotation concentrates. Enargite, the sulpharsenate of copper, is easily recovered by flotation. Flotation of arsenical ores offers no particular problem although occasionally extremely fine grinding is required to release the mineral. The ratio of concentration is generally low and in areas remote from smelters the flotation concentrates are roasted. Arsenic is passed off to atmosphere or collected and the resulting calcines are treated by the cyanidation process for extraction of gold. Under favorable circumstances arsenical-gold concentrates are shipped direct to smelter.
Flotation of arsenical ores with “Sub-A’s” is quite extensively applied in several sections of Canada, United States, Australia and South America. Flowsheets as described above were also in use in the Philippines.
Tin Flotation
The chief sulphide of tin is stannite and although it is relatively rare, it is being successfully concentrated with “Sub-A’s” in Bolivia. Flotation plays an important part in the concentration of cassiterite, the oxide of tin. Sulphide concentrates, usually iron, are removed by flotation ahead of the subsequent gravity concentration of cassiterite. This is being done with supercharged No. 30 and No. 24 as well as the No. 18 Special and smaller sizes, in Bolivia, British Columbia, USA and Argentina.
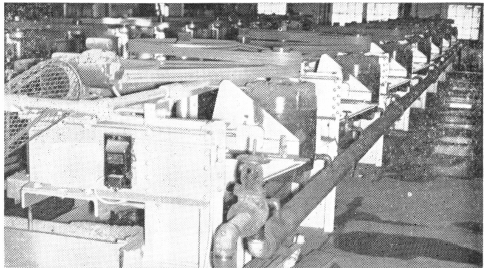
Cobalt Flotation
Complex cobalt sulphides and arsenides are recovered with Flotation Cells in Belgian Congo and Ontario, Canada. The main problem in satisfactory recovery is close operating control. Controlled aeration of the pulp is very important when floating this mineral for it is usually associated with other sulphides.
Precious Metal Flotation
The precious metals, silver, gold and platinum are frequently found associated with sulphides, arsenides and other complex ores. Flotation of these sulphides and arsenides is extensively used, particularly silver ores. Gold tellurides are frequently found present in these complex mixtures and are recovered in the flotation concentrates.
For the concentration of precious metal ores, many localities are using on account of their selectivity and high ratio of concentration. Among the more prominent districts are Idaho, Colorado, Mexico, Bolivia, British Columbia, Ontario, Quebec, Australasia, Africa and Russia.
Oxide Flotation
Flotation of oxidized metallic ores presents quite a problem, although as a result of technological developments during the past few years much has been accomplished toward its general usage. Where conditions permit, gravity concentration is still extensively employed; however, slime losses are high and flotation on this fraction is advancing the economic return.
The treatment of oxidized ores has not reached the advanced stage attained by sulphide and precious metal flotation due chiefly to the relative scarcity or confinement to superficial deposits. Oxides due to their dull luster are more difficult to float than the more lustrous sulphides.
In areas favorable to oxidation there is a tendency toward surface enrichment and as the ore body is developed it is not far before it grades into the sulphide zone. In the oxide zone the metals are generally in the form of carbonates and sulphates, both of which are considered in the general classification of oxides.
Oxide Copper Flotation
Flotation of oxide copper ores finds its most wide use in the Congo and Rhodesia sections of Africa. Malachite is the copper mineral recovered by Flotation in these areas. Flotation of these ores presents both mechanical and metallurgical problems which, by careful analysis by the metallurgists in charge, have been overcome. In the flotation of copper oxides, reagents play a very important part and the correct computation, coupled with efficient mechanical control, have been brought to a high degree of perfection by the operators, especially in Africa but also in South America and sections of the United States. In practically all these areas the“Sub-A”, with special mechanical features adapted to the problems involved, is playing an important part. A new development in reagent combinations, which gives off nascent hydrogen, is in some cases proving to be an important factor in floating these oxides.
Flotation of Industrial Minerals
By far the greatest field for flotation lies in the treatment of non-metallics which are just coming into prominence in various localities of the world. Advance in flotation technique and development of new reagents, especially the cationics, have contributed much toward establishing froth flotation as the accepted and standard method to separate and concentrate a wide variety of non-metallic minerals. Gravity methods in many instances cannot be applied to these minerals for quite obvious reasons and until the advent of flotation no feasible method of separation was available. The trend now is definitely flotation of non-metallics and it may not be long before the total tonnage of non-metallic flotation surpasses that of metallics.
In the field of non-metallic flotation the “Sub-A” Machine is playing a very prominent part and will continue to do so as the technique is applied to other branches of this field. They are so widely accepted for non-metallic work that for some minerals they are practically exclusively used.
Fluorspar Flotation
The great demand for high-grade fluorspar, in particular that meeting the specifications for ceramic and acid grade, has been met, in part at least, by flotation, the most important recovery method. In the early days of fluorspar milling, hand sorting, decrepitation and gravity methods were employed almost exclusively and supplied the demand for the metallurgical, ceramic, and chemical trade. In more recent years the demands were greatly increased, particularly for acid grade spar which is now principally used for manufacturing of hydrofluoric acid and in connection with production of high test aviation gasoline, refrigerants, etc. This, coupled with depletion of high-grade ore reserves and necessity of working more complex deposits, resulted in adoption of flotation by the industry.
Flotation of fluorspar in general is about as well established as is the flotation of sulphide minerals. The progress made in recent years has resulted in its universal acceptance. Although reagents are more or less the same as those used in the first commercial fluorspar flotation plant installed over 20 years ago in one of the large Canadian mills, certain refinements have been made, and it is now possible to treat some of the more complex ores heretofore too difficult to treat successfully.
One of the most important factors in fluorspar flotation is the selectivity so necessary when making acid grade which in most cases must contain less than 1.5% silica. It is often necessary to clean a large bulk of concentrates several times in order to attain ultimate grade. Flowsheets are now quite common where 7 or 8 cleaning steps are in use. The “Sub-A” Flotation Machine is universally used in the fluorspar field and fully 95% of the present day production of acid grade fluorspar is being produced with. Its special construction features such as the gravity flow principle and multi-cleaning stages within the machine have contributed greatly to the success being obtained in this field as is evidenced by its wide use in the principal fluorspar districts, particularly in Illinois, Kentucky, Colorado, New Mexico, Newfoundland, Canada, and Mexico.
Post-war demands for new products and new uses in which fluorspar plays an important part will result in further development and improvement in the flotation of this now vital war mineral. Heating flotation pulps is now common practice in many of the fluorspar plants and this has resulted in certain benefits, particularly in improving final grade and overall recovery.
Talc Flotation
The mineral talc is found associated with several varieties of gangue material and the flotation process is the efficient and accepted means for production of talc concentrates. In these flotation separations it frequently happens that gangue rejection is a valuable by-product.
Talc flotation concentrates are used chiefly in the cosmetic, varnish, lacquer and ceramic industries. The grade specifications for these industries are exacting and the mesh analysis usually required is 99% minus 325. Flotation is the only effective means to produce acceptable grade as the ratio of talc in the feed in most cases is extremely variable. Beneficiation by flotation gives a uniform product which, after final grinding, is ready either for shipment or blending to meet varying market specifications.
In general, talc flotation is preceded by a dry mill recovery circuit which scalps off the high grade. Such a circuit will not meet the demand of changing market requirements and the recovery is low. Flotation, operating as a scavenger circuit, produces a superior product from a former waste. This circuit is operated according to market conditions. “Sub-A” Flotation is used extensively for talc flotation and while talc flotation is relatively simple with standard reagents, nevertheless the readily adjustable is a valuable facility for controlling production.
Flotation of talc has been successfully carried on in Vermont and New York, as well as in Canada, Africa, England and the Russia.
Phosphate Flotation
By far the greatest present application of flotation in the non-metallic field is in the recovery of phosphate. In the United States, Florida is the best-known district where flotation is being applied on a large scale. Washing, screening, and classification are the common methods for recovering the coarse and pebble phosphate, but it remained for flotation, and to a certain extent agglomerate tabling, to provide a satisfactory and low-cost means to reclaim and beneficiate phosphate formerly rejected as tailing.
Prior to the war a large percentage of domestic production of phosphate was exported for use chiefly as fertilizer. The trend in recent years has materially altered this situation due primarily to an extensive program on the part of the principal phosphate producers to educate the public along the lines of soil conservation and increased production. As a result, phosphate fertilizer production has actually increased in spite of temporary restrictions on foreign trade. This increased demand has more or less forced full utilization of existing treatment methods and the trend is definitely toward flotation by the more progressive phosphate producers.
In the flotation of phosphate it is generally the practice to handle coarse deslimed pulps minus 14 mesh and finer. Silica is the chief impurity to be eliminated and its removal is accomplished by either floating the phosphate with fatty acids or by floating the silica with cationic reagents such as the amines. In some cases it is more economical to employ a combination of the two processes in order to attain maximum grade and recovery.
Phosphate, being coarse and fast floating, requires a machine capable of handling large tonnages at a high density. For this purpose the “Sub-A” Flotation Machine has found wide acceptance and is in general use not only in the major phosphate districts of the United States, but also the Russia, South American and other localities. Due to the usual low ratio of concentration, large tonnages of mineral bearing froth must be removed from the cells and for this purpose the double overflow “Sub-A” is the choice of the industry. Another feature, aside from ability to handle coarse material, is the adjustable sand relief openings with controlled circulation of pulp from cell to cell. This feature has made it possible to handle extraordinary high tonnages without impairing the usual operation of the machine or reducing its metallurgical efficiency.
The No. 24 (43×43) “Sub-A” with double overflow is quite commonly used in phosphate flotation and it is not unusual for tonnages in excess of 1000 tons per 24 hours to be handled through one of these machines. The present trend is toward the larger No. 30 (56×56) “Sub-A” Flotation Machine, having double the volume and capable of handling twice the tonnage of the No. 24s.
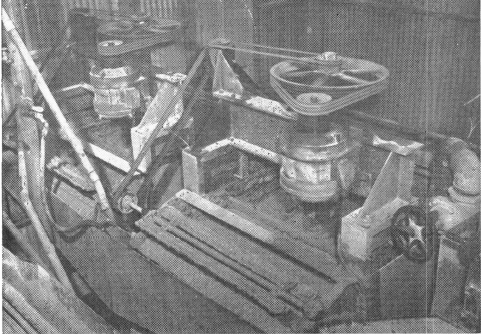
Manganese Flotation
Recovery of manganese minerals, because of their generally high gravity, is for the most part accomplished by gravity methods employing coarse and fine jigs and tables. Practically all manganese minerals are soft and therefore losses by gravity methods leave considerable to be desired insofar as recovery is concerned. Then, too, some manganese ores are not amenable to gravity methods due to close association with impurities. This, of course, necessitates grinding, in some instances quite fine.
Manganese flotation has been successfully employed for several years, although only on certain specific ores where the necessary research and experimental work developed the art to a point where it could be economically applied. In general, manganese minerals are floated from the gangue impurties by what is known as “soap flotation”, except for certain modifications. Slimes sometimes interfere and it may be necessary to discard them, at least in part, prior to flotation, in order to make reagents effective and maintain costs at a minimum. Flotation of manganese minerals has been commercially applied in Cuba, the U.S.S.R., Minnesota, Montana, New Mexico, and several other localities. In many of these operations other methods are employed in conjunction with flotation in order to attain desired results. For example, in Cuba the flotation concentrate requires calcining or sintering for maximum grade and to meet size specifications.
In Montana the manganese carbonate, rhodochrosite, must be calcined to break down the carbonate to the higher grade oxide.
One of the South American ores, which has been treated, required quite fine grinding in order to liberate the gangue mineral, calcite. This, of course, slimed the softer manganese oxides appreciably. In this case, however, a reagent combination was developed which successfully depressed the manganese and floated the calcite. Recovery and grade were exceptionally favorable. Some of the newer surface- active reagents are showing promise and undoubtedly their successful application will contribute toward solution of the more or less difficult problem of applying flotation to manganese ores in general.
Mica Flotation
New developments in recent years have greatly expanded the uses for mica. Fine ground mica, in particular, is much in demand for roofing, as a filler in paint, and synthetic rubber, as well as various other industrial applications. In the past, the greatest source of supply for this valuable non- metallic has been as a by-product from clay-washing plants and from grinding up scrap mica.
Flotation has been applied commercially and is now successfully used for recovery of coarse and fine mica from clay and feldspar ores. It has naturally alleviated the shortages by reclaiming this valuable mineral from mill products heretofore considered as waste or tailings. In treatment of pegmatitic ores for recovery of such minerals as quartz, feldspar and spodumene, a small but important amount of mica must be removed and this is most conveniently done by flotation, sometimes at a relatively coarse size.
“Sub-A” Flotation Cells have been used for mica flotation since the early application of flotation in the mica industry. As the industry expands it will contribute materially to this branch of non-metallic flotation due to the exclusive features of the “Sub-A.”
Tungsten Flotation
Until recent years gravity has been the accepted method of concentrating tungsten ores. While gravity concentration produced very acceptable grades, in most cases the recovery was low on account of the “easily slimed” characteristic of scheelite, the chief ore mineral for tungsten. Furthermore, while gravity concentration can produce acceptable grades as far as tungsten content is concerned, marketable concentrates have other rigid specifications difficult to maintain by gravity methods only.
The recent application of flotation to tungsten concentration has resulted in improved recoveries which consequently widened the range of ores that could be economically handled. Flotation is usually used in conjunction with gravity as a scavenger operation to recover slimed scheelite. In general, gravity means are used to recover coarse scheelite and/or wolframite at a coarse grind. Concentrates thus obtained are, if required, raised to market specifications by flotation for removal of impurities such as sulphides and free mineral. A further grading of gravity concentrates is obtained by leaching for removal of non-metallic constituents. Magnetic concentration is also extensively used for removal of high gravity material such as garnet.

Flotation is also extensively used in tungsten milling for removal of iron and other sulphides ahead of the actual application of flotation for concentrating the tungsten mineral. The grade of tungsten flotation concentrate produced is dependent on the type of ore being treated but in most cases the grade is too low to satisfy market requirements. In ores containing considerable amounts of calcite and other carbonates, grade is a problem, especially where the mineral is finely disseminated. In siliceous ores free from carbonates a fairly high grade concentrate can be produced. In either case flotation concentrates are raised in grade by gravity or direct chemical treatment.
“Sub-A” Flotation is quite extensively used for scheelite concentration. They are used for cleaning gravity concentrates, removal of iron and other sulphides prior to scheelite flotation and for producing scheelite concentrates. In the treatment of tungsten ores recovery is obtained at as coarse a mesh as possible; consequently Cells are valuable for their ability to handle a coarse feed without short circuiting. Furthermore, due to the selective action there is a maximum rejection of carbonates.
Coal Flotation
In practically every coal washing plant a problem exists concerning disposal or making use of the fine coal in the waste wash water. In years past this material was allowed to be wasted and in some instances has polluted streams to an alarming degree. Fine coal and its accompanying ash or sand has been known to fill stream and river channels to the extent where they had to be dredged. Some method of proper handling and disposal, therefore, became imperative and in some districts flotation has been a solution to the problem; at least, enough fine coal could be reclaimed to permit economically adequate disposal of refuse.
The problem in coal flotation is ash removal. In most coal washery refuse the ash is quite fine and free, although a considerable amount may also exist in what may be called the sand fraction. Washery refuse is generally quite dilute, 4 to 5% solids, and in the process of thickening partial desliming is usually practiced to eliminate the high ash slimes, and the result is that the thickened product is more amenable to flotation. Coal as coarse as 8 or 10 mesh has been floated, but it is more desirable to screen out the coarser sizes. In general, coarse coal is low enough in ash to be considered a finished product, and, therefore, need not be handled by flotation. Often it may not pay to remove the coarse products and here the “Sub-A” will handle the entire feed, selectively floating out the desired portion with freedom from operating troubles.
Coal responds very well to flotation with a minimum amount of low cost reagents such as fuel oil, pine oil, and cresols. Pulp and froth handling is somewhat of a problem, particularly in circuits with multi-stage cleanings by reflotation. The “Sub-A” Flotation is used almost exclusively in the coal flotation field due to its exclusive features in regard to pulp handling, recirculation of middling products, and its ability to make a product with low ash. Large tonnages are being handled in these machines particularly in Pennsylvania and to an increasing extent in Alabama and other parts of the United States. In England and Continental Europe coal flotation is quite extensively used. At present the United States and Canada lag behind the European countries, but indications are quite likely that the field will be expanded more extensively as some of the new developments in coal flotation and markets for the resulting product become better established.
Feldspar Flotation
Due to the gradual depletion of high-grade deposits of feldspar and felspathoid minerals and more rigid marketing specifications, flotation has come to the foreground as a commercial concentrating process in this non-metallic field, so important to the glass industry. The usual impurities in feldspar ores are mica, quartz, sulphides, iron oxide and to a certain extent garnet.
After extensive research programs over the past several years by various investigators, a fairly dependable reagent combination has been developed to effectively depress quartz from feldspar, thus permitting the latter to be floated. This reagent combination, making use of hydrofluoric acid as the quartz depressant, still leaves much to be desired insofar as costs are concerned.
Feldspar ores in general are quite abrasive and as a rule must be concentrated at a coarse size because of marketing specifications. The usual specifications are minus 20 mesh with not over 10 to 15% minus 200 mesh. In addition, due to the necessity of using hydrofluoric acid, pulps are corrosive from an acid pH as low as 2.5. The “Sub-A” Flotation Machine with certain modifications to meet these special conditions, in the laboratory and experimental pilot plants, has contributed much toward putting feldspar flotation on a commercial basis. Its selective action and ability to handle coarse sands without short circuiting are its outstanding features in this field. Molded rubber wearing parts also reduce abrasion to a minimum.
Feldspar ores are now being treated commercially in California, Tennessee, North Carolina, and experimentally in several other localities. The next few years will see considerable progress in this field and undoubtedly some of the present difficulties will be overcome.
Clay Flotation
Many of the high-grade clay and kaolin deposits are gradually becoming depleted, thus leaving lower grade, off color, heretofore undesirable material as the chief source of supply. In recent years considerable experimental work has been done by various investigators indicating the feasibility of not only using flotation as a means of improving the color of various clays, but also in fractionating them into ceramically different products. These developments are making it possible to consider mining former deposits which did not come up to specifications and by so doing has greatly increased workable ore reserves.
Some recent work on clay flotation has shown that exceptionally, white products can be produced by floating out the colored impurities as a waste product. One of these plants is now going into operation in the United States and will be equipped exclusively with “Sub-A” Flotation Machines. This development is being watched with interest as it may be the forerunner of an important non-metallic application for flotation.
Silica Sand (Quartz) Flotation
The glass industry demands a reasonably high-grade quartz sand low in impurities such as iron oxide and alumina. Manufacture of optical glass in particular requires an exceptionally pure sand. A source of supply close to the market is usually necessary due to the low dollar value of this important ingredient in glass making. It is, therefore, imperative to develop conveniently located deposits and reclaim as much of the marketable sand as conditions will justify. Washing and classification in the past have been the main methods in working sand deposits.
Flotation of various non-metallics such as feldspar and spodumene from pegmatitic deposits invariably produces quartz as a by-product which can usually be marketed at a profit. On certain beach sands fractionating them into low and high alumina products is now being accomplished commercially by flotation. “Sub-A’s” are also in successful operation in one of the large eastern plants producing silica sand of optical grade by a special process in which almost complete elimination of the detrimental iron oxide is being attained. Other plants are also going into operation and significant is a complete “Sub-A” Pilot Plant for one of the South American Republics. Flotation may, to a large extent, replace former costly methods of purification and undoubtedly will make it possible to consider handling some of the heretofore marginal deposits.
Silica sand is perhaps one of the most difficult materials to handle in a flotation machine due to its abrasive action on wearing parts. The “Sub-A” Flotation Machine, equipped with molded rubber wearing parts, standard for many years, is ideal for just such a condition and in addition, will efficiently handle the granular slime free pulps usually encountered.
Cryolite Flotation
The flotation process has been successfully applied to the beneficiation of cryolite ore. In this work “Sub-A’s” are used for roughers and several stages of cleaning. Flotation of cryolite requires high selectivity for a maximum rejection of gangue impurities. Several stages of cleaning are necessary to attain acceptable grade and this is attained on a machine with recirculation of middling by gravity.
Fatty acids are used for collectors of cryolite, usually after the removal of sulphides. In cryolite flotation a high alkaline circuit is necessary for satisfactory results.
Graphite Flotation
Graphite is perhaps one of the easiest non-metallic minerals to recover by flotation because of its natural flotability and water repellent action. It has been successfully floated as coarse as 10 mesh, which contributes much to the market value. Flake graphites are sold according to size with the coarser sizes commanding the highest prices.
“Sub-A” Flotation Machines have long been considered standard for treatment of graphite ores. These machines have been in successful operation in Norway, Sweden, the United States, and to a lesser extent in other localities. The Unit Cell has been quite successfully applied for recovery of coarse graphite, particularly from the grinding circuit or from ores after coarse crushing. Pulps are usually handled at approximately 10 mesh without any difficulty through “Sub-A” Flotation Machines and maximum grades are produced with a minimum number of cleaning steps.
In the Alabama, Pennsylvania, New York, and Texas areas, “Sub-A” Flotation Machines are widely used and in all of these operations a large percentage of the production was in the premium grades of graphite. Preserving the flake as coarse as possible by careful treatment through the crushing, concentration, drying and sizing steps calls for a well-designed plant and flotation equipment, such as the “Sub-A”.
Bauxite Flotation
The most important present-day commercial source of aluminum is from the mineral bauxite, a hydrous aluminum silicate, which usually has a variable composition and is associated with such impurities as clay, silica, iron oxide and titanium oxide. Present day production is generally from high-grade deposits and concentration depends to a large extent on washing plants to remove clay and other impurities.
The U.S. Bureau of Mines and other organizations have undertaken extensive research programs in recent years to work out a commercial beneficiation method. Flotation has shown the greatest promise in the field. A completely equipped Pilot Plant of a semi-commercial size has been erected in the Arkansas Bauxite district and it is expected some interesting developments will be forthcoming as a result of this installation. “Sub-A’s” are being used exclusively in this important project.
Magnesite Flotation
Magnesite, the magnesium carbonate, is usually found associated with limestone and dolomite. Impurities consist of varying amounts of talc, serpentine, iron oxides and silica.
Magnesite is used in the production of refractories, cement, rubber, insulation, building materials, magnesium salts, and magnesium metal. The widespread demand for the latter in recent years has created a considerable magnesite industry in which flotation has been the means employed for beneficiation. As flotation is relatively new to this field there has been much research work conducted as to the best reagents and method of applying flotation. Several types of flowsheets have evolved, such as direct flotation of classifier overflow for production of a magnesite concentrate with several cleaning stages required. A modification of this circuit is a desliming section prior to flotation for removal of slime impurities. A further trend has been directed toward removal of the insoluble constituents by flotation, leaving the magnesite concentrated in the tailing, and production is being obtained with this flowsheet. Magnesite is also obtained as a by-product from the flotation of talc, which in this case is the predominant constituent of the ore.
Accurate reagent and pH control are essential in magnesite beneficiation and a dispersing reagent is usually employed to prevent a circulating load of slimes from the several cleaning stages. Desliming ahead of flotation minimizes this latter problem as well as materially reducing reagent costs, giving a more uniform flotation feed and a stable froth condition. Pulp temperature is a further limiting factor.
“Sub-A’s” are used for magnesite concentration in several localities where they are noted for their ability to recirculate products for recleaning without the use of pumps. In addition, the selectivity facilitates the production of a low lime concentrate.
Magnesite is produced in Canada, Nevada, California, Vermont, Washington, Russia, Greece and several other regions. A portion of this production is used direct and concentration is employed only when a high-grade product is required.
The magnesium hydroxide, brucite, is also used for magnesium production and flotation has been applied to the concentration of this mineral.
Iron Ore Flotation
The concentration of iron ores has received widespread attention in recent years and many iron ore producers as well as certain state and government agencies have in progress extensive research programs investigating various methods of concentration. Although magnetic separation, classification, and gravity methods have been well established in this field, flotation is gradually gaining prominence. Not only can a higher grade concentrate be produced by flotation but heretofore unworkable deposits are amenable to this process. Many iron ores contain impurities which can be removed by flotation making it unnecessary to add as many scavenging fluxes in the smelting furnaces. What you remove at the beginning you need not worry about at the ending. A typical example of this is the taconites, in the Minnesota Iron Ranges. It is estimated that in the Mesabi Range of this district 60 billion tons of low-grade, closely associated, semi-magnetic taconites are available. Fine grinding, in some instances to 200 mesh, is required to liberate the silica from the iron oxide and consequently the importance flotation will play in the future of this district is quite evident.
The “Sub-A” Flotation Machine is extensively used, both in laboratories and semi-commercial plants now working on iron ore flotation. Because of the large tonnage operations under consideration, it is quite evident that the No. 30 “Sub-A” Flotation Machine, capable of handling at low cost well over 1500 tons and in certain cases up to 3000 tons per 24 hours, will be the choice of this important field due to its widespread success in other similar large tonnage fields. Plans have also been completed for an even larger tonnage machine in anticipation of the industry’s demands.
Research checked by semi-commercial operations has definitely established the economics of flotation in iron ore concentration and reliable estimates indicate that workable ore reserves in the Minnesota, Alabama and other iron producing districts can be extended many decades, even at the present high rate of consumption.
Titanium Flotation
The general application of titanium compounds in alloys, pigments, welding rod, and chemical warfare has created quite a demand for such minerals as rutile and ilmenite, the chief sources of this important element. Gravity, magnetic and electrostatic methods have been employed in years past in supplying the market for this important non-metallic, principally from deposits in which the minerals occur in granular size. The urgency of increasing production and the necessity of working lower grade, more complex deposits, has prompted the use of flotation in this field. Extensive research programs have been in progress for the past few years and some very encouraging and economical flotation treatment methods have been developed.
In 1943 when the demand for titanium minerals was most critical a large plant employing “Sub-A’s” was put into operation on the beach sands of one of the southern states. This plant handled approximately 3000 tons of sand per 24 hour day through a bank of No. 30 “Sub-A” Super charged Flotation Machines and was very satisfactory metallurgically. Outstanding mechanical performance of the was attested to by their efficient handling of deslimed granular sand at pulp densities in excess of 60% solids. “Sub-A” Flotation is now being installed in one of the large eastern ilmenite concentration plants to recover this valuable mineral now being lost in fine tailings from the gravity concentrator.
Soap flotation following special acid treatment and washing is the common procedure in non-metallic flotation of titanium minerals, although other combinations and cationic reagents are also showing favorable possibilities. Relatively high-grade ilmenite with a minor amount of silica usually is treated by floating the latter with amines. Selectivity is important in this work and in this respect the “Sub-A” has definitely shown itself unsurpassed.
Barite Flotation
The oil industry makes use of a tremendous tonnage of barite in its drilling operations. In order to drill deep wells under high gas pressure a weighting material in the drill holes must be used which is not only heavy but also free flowing at high density and chemically stable when pumped at high pressure down through several hundred feet of drilling tools. Barite being inert to acids and having a relatively high gravity, is well suited for this purpose and because of this, in recent years, the demands of the industry have greatly increased. Practically all of the commercial deposits of barite require concentration in order to meet the grade specifications.
The oil industry prefers a product with a specific gravity of at least 4.25, while the paint, rubber and chemical industries prefer a higher grade product.
Gravity methods have long been used in concentration of barite ores; however, due to their softness, slime losses are high and recovery is generally low. Some of the deposits are not amenable to gravity due to close association with the common impurities such as silica, lime, iron oxide, and sometimes calcium fluoride. Barite ores are easy to float and since marketable products are generally most desirable in a finely ground condition, flotation has established itself as the standard method of treatment.
General practice is to grind to all minus 325 mesh, float the barite, and then dry at high temperature. This applies when floating the barite with fatty acids. Cationic reagents are also used to float impurities from barite and in this case it is usually satisfactory to dry at low temperature as such reagents are largely removed in the froth and consequently do not exert any harmful physical effect on the barite product.
“Sub-A” Flotation Machines are used exclusively in the barite flotation industry. The most notable district is the Arkansas field where two large plants have been in successful operation for several years. The general increased demand for barite, particularly by the oil industry, will undoubtedly see a considerable increase in present plant capacity and new installations within the near future.
Spodumene Flotation
Spodumene, a lithium aluminum silicate, is a feldspathoid mineral, which has come into prominence as the chief source of lithia. Lithium metal salts are in much demand in air conditioning systems, special greases, and various other uses by the chemical, metallurgical, ceramic, and process industries, all the way from controlling atmospheres in heat treating metals, to flavoring cigars. There is very little gravity difference between spodumene and its associated minerals such as quartz, mica, and feldspar, and aside from hand-sorting and selective mining, flotation is about the only economical and practical concentration method.
Plants are now in commercial operation in South Dakota and North Carolina and “Sub-A” Flotation Machines have played an important part in developing the successful operations in this non-metallic field. Like quartz and feldspar flotation, coarse, slime-free pulps must be handled and it is usually essential to make a two or three-product flotation separation with multiple cleaning steps. For example, mica must be removed first, then the spodumene, and finally the feldspar, if it is present and economical to separate from the quartz passing to tailing. This circuit calls for utmost flexibility in flotation equipment and very careful control in pulp conditions and reagents in order to obtain a sharp split between the individual minerals which may be present.
Other spodumene plants are under consideration and with the gradual development in flotation technique in this relatively new field it is anticipated the normal demands for lithium products will be met without difficulty. Some of the new post-war uses, however, may further spur the efforts of the present producers.
Sulphur Flotation
An excellent example of a non-metallic ore treated by flotation is sulphur. Elemental sulphur has been successfully concentrated by flotation, and commercial plants have been operated in Utah, California, Chile, Palestine and U.S.S.R. The process is also under consideration for plants in Turkey and South America.
In sulphur flotation the chief problem is the rejection of iron and insoluble material. In general, concentrates with over 90% sulphur can easily be obtained with the selective “Sub-A”. Most sulphur ores are acidic and special machine construction is required. However, the standard rubber-protected wearing parts of the “Sub-A” are quite satisfactory for this condition. Also, alloy steel plates or even wood tanks can be used when corrosion is an item.
Nepheline Syenite Flotation
Nepheline Syenite, a silicate high in alumina and sodium, has a number of unusual properties which make it especially desirable for the ceramic trade. It fuses at a low temperature, has a wide sintering range, and is excellent for blending with low alumina feldspars and other non-metallics which are used extensively in the manufacture of glass, porcelain, and innumerable products of the ceramic industry.
Impurities such as mica and magnetite are usually associated with nepheline syenite and must be removed before the latter can be considered satisfactory for general use. As for other non-metallics, flotation finds a general application here in removing these impurities, although the nepheline-syenite industry is at present limited and controlled. The “Sub-A” Flotation Machine is now being used in the only known operation in the United States which, incidentally, secures its ore from eastern Canada. In this operation the ore is ground to approximately minus 24 mesh and the impurities removed by froth flotation with the usual reagents for non-metallics.
Salt Flotation
Flotation has been successfully used in Canada for removal of impurities from sodium chloride. In this particular case anhydrite and gypsum are recovered in a flotation concentrate which is dis-carded to waste, while the tailing is a high-grade salt product free from impurities. A similar problem in the United States has also been successfully Solved by flotation.
Considerable research has been conducted toward advancing the separation of crystallized salts. In all this work flotation has taken the leading role and records indicate that it has been successfully applied in various sections of the world. Separation of salts by flotation is of major importance as it reduces or replaces expensive fractional crystallization processes.
Flotation is important for this work as these cells are able to handle a coarse feed with positive circulation. Furthermore, Cells can be furnished with the special corrosive-resistant materials necessary to counteract the conditions encountered.
Potash Flotation
Potash is one of the principal plant foods necessary for the growth of most vegetables, grains, and fruits. In addition, it has various other important uses in the chemical field. For many years North America depended entirely upon foreign countries for its source of potassium compounds. In the last 20 to 25 years, however, local production of potash has gradually increased and is now a major industry.
Immense deposits of potash bearing salts are known to exist in various localities of the United States and notable among these are the ones in New Mexico, Utah, California, and Texas. The usual method of separation has been by fractional crystallization, which generally required an elaborate outlay of equipment as well as being expensive to operate and maintain. It remained for the introduction of flotation in this field of concentration to provide a satisfactory solution to the many problems confronting the industry.
The principal potash mineral is sylvite, a chloride of potassium (KCl). In brines and salt deposits it is associated with sodium chloride (NaCl). The problem, therefore, is to separate these two salts, and since both are water soluble the operation must be carried out in a brine saturated with respect to both of the salts. Flotation is at present being successfully used either to float the potassium chloride or sodium chloride, depending on local conditions and requirements. Crude salts which must be mined are crushed and ground in the usual manner before flotation treatment. On the other hand, brine from the Great Salt Lake area in Utah is increased in potash content by fractional crystallization, making use of solar heat to do the evaporating. After the potassium concentration is up to a high point, the entire lake area or pond of enriched KCl brine is allowed to crystallize. The resulting salt is then mined, ground, and subjected to flotation in the usual manner to produce the final high potash product ready for conversion into fertilizers and special potassium chemicals.
“Sub-A” Flotation has played an important part in the development of this important industry which now has become definitely established in the United States as well as in foreign countries. “Sub-A’s” are being used in the potash fields of New Mexico and also in the operation on the Great Salt Lake in Utah. The selective action in the “Sub-A” and its ability to handle a coarse feed makes it the ideal machine for the separating of these salts.
Cement, Limestone and Flotation
In the preparation of cement the ingredients are mixed in definite ratio depending upon ultimate use whether for masonry, highway construction, building construction or construction of large dams. Physical characteristics to meet practically any condition can be controlled in cements by proper selection of raw materials of which lime-stone is of prime importance. Enormous quantities of this ingredient are required by the cement industry and consequently the problem of uniformity was in general a serious one confronting the industry.
The introduction of flotation in the field of limestone beneficiation has definitely resulted in superior cements as raw materials can be fractionated and recombined almost at will. Limestone rock is now being treated by flotation in United States, South Africa, Argentina, France, and in Finland. Notable among these operations is the one in Pennsylvania. In this operation graphitic impurities are floated out and discarded to waste. The resulting finely ground and deslimed pulp is further fractionated by flotation into high and low silica-lime products, stored, and recombined as required.
Flotation, now a major concentrating process in the cement industry, is likely to become as important in the non-metallic field as present day phosphate concentration. With the more general application of cationic reagents, former difficulties are being overcome and naturally this development is contributing to the widespread success of flotation in this important non-metallic industry. The important part “Sub-A” Flotation has played in non-metallic beneficiation is world-wide and its adaptability to various flotation problems is indicative of complete acceptance.
Miscellaneous Non-Metallics Flotation
Various non-metallic minerals such as beryl, chromite, corundum, garnet, gypsum, kyanite, sericite, sillimanite, zircon, etc., are at present receiving the attention of various investigators. Satisfactory application of flotation in concentrating these minerals, in most instances, is now beyond the laboratory stage. In view of the general commercial application of flotation to the minerals previously mentioned in detail, these latter miscellaneous non-metallics, no doubt, will be creating more interest as the demand for their use increases. Although flotation has made some important advances in the non-metallic field in recent years, the future trend undoubtedly will be towards wider use, reagent development and lowering of treatment costs.
Industrial Flotation
Flotation is being used for concentration and beneficiation on such a wide scale for metallics and non-metallics that its worth is being recognized in other fields. In recent years experimentation and research have opened up new applications where flotation can be of material benefit. It is often said that if two different particles are physically separated in a mixture, flotation can make a distinct commercial separation. Industries other than mining are becoming familiar with the flotation process and it is now being used on a commercial scale in several of these industries. There will undoubtedly be more general use of this “tool” as its value becomes more generally realized, and developments are advanced. Industry has become flotation minded and much experimental work is being conducted with flotation, directed toward advances in various industrial procedures, especially since the possible use of coarse as well as fine flotation is realized.
“Sub-A” Flotation Cells with their distinct gravity flow of circulation are being used for several industrial applications and in this work they are leading the way for more general use of the flotation process. find a ready acceptance in these industrial fields as in most cases very accurate control is required, especially in respect to aeration, which must be closely controlled.
Industrial application of the flotation process is outlined briefly in the following specific references.
Rubber Flotation
Events in recent years have directed the attention of research men to the possibility of extracting rubber from plants which could be obtained locally. Excellent work along this line has been conducted by the National Research Council of Canada. Results obtained show that resin-rubber can be successfully concentrated from the common milkweed with an extraction of 90%. The method evolved for this work includes cooking milkweed leaves in dilute alkali, washing and filtering out dissolved materials and then agglomerating the resin-rubber in a pebble mill. The mill discharge is passed to a 60-mesh vibrating screen with oversize returning to the mill and undersize to Flotation for concentration and cleaning of the resin-rubber in the froth. The cleaned concentrate is thickened and then passes to an agglomeration stage followed by drying.
In resin-rubber flotation the slurry fed to flotation contains its own frothing and collecting reagents. Frothing depends on the pH of the washing cycle and pulp density for flotation is less than 2% solids.
Bituminous Sands Flotation
Flotation can, in general, be used satisfactorily for recovery of various bituminous substances such as bitumen, tars, asphalts and asphaltic minerals. Research work along these lines has been carried on for a number of years, and more recently, operating plants have worked with a certain degree of success for the recovery of bitumen. In this work accurate aeration control together with a scouring action is essential.
Pilot plant flotation work has indicated distinct possibilities for applying flotation to bituminous and oil substances.
Grains Flotation
Beneficiation of grains by flotation is a recent revolutionary application of the flotation process. This has been successfully applied on a fairly wide commercial scale to the beneficiation of wheat prior to grinding in flour milling.
The adaptation of flotation to grains, and especially wheat, has been a development of widespread interest which promises to become a major factor in future wheat and grain milling operations. The process for wheat involves the removal of the two or three outer skins (beewing) of the bran in Flotation Cells especially designed for this purpose. These cells, which are a modification of the standard “Sub-A”, are termed “peeling” cells. They are an application of suppressed flotation and the chief function is agitation for a fixed period for loosening the outer bran coats. This peeling process is facilitated by the impact action between rubber impellers and wearing plates.
The wheat from the peeling unit passes to the “Sub-A” Flotation Machine where the pulp is subjected to action similar to the peeling circuit, as well as aeration and frothing. The latter action carries the “beewing” to the surface where it is rejected to waste as a flotation concentrate. The peeled wheat from the flotation cells is dewatered on a vibrating screen and a continuous centrifuge, followed by a drying, aspiration and tempering cycle. The wheat is now ready for grinding and processing into Earle Process flour.
The “Sub-A” Cells used for grain work are of special design in which are incorporated features to take care of the unique requirements of grain peeling. The time of control is an important factor as well as accurate aeration control.
The application of flotation to the flour milling industry bids fair to become a major achievement in the processing of wheat for human consumption. This new method effectively removes the indigestible outer layers of wheat prior to its introduction to the “milling” system. The flour derived from this new process is a naturally enriched superior product 100% flour.
eScrap Recycling by Flotation
Flotation has also been used for such other industrial problems as purification by flotation for removal of colloidal precipitates or suspension. Waste water from paper mills has been subjected to flotation for recovery of fiber, and possibilities for further application in this field look promising.
Industrial Waste Flotation
The use of Cells for cleaning up floor wastes, refuse for many industries, and chemical plants is being rapidly extended. The removal of ink from print paper has great possibilities. In other words the use of flotation through the mechanical perfection of the “Sub-A” Cell is unlimited. One should resort to flotation testing in solving the many industrial and metallurgical problems.
Source: This article is a reproduction of an excerpt of “In the Public Domain” documents held in 911Metallurgy Corp’s private library.